Содержание
Введение. 3
1. Теоретические основы организации и нормирования труда многостаночников 5
1.1. Организация труда многостаночников. 5
1.2. Нормирование труда многостаночников. 10
2. Проектирование норм труда при многостаночной работе. 18
3. Определение эффективности проекта. 26
Заключение. 26
Список литературы.. 26
Введение
Выбранная тема курсового проектирования – проектирование норм труда при многостаночной работе. Актуальность выбранной темы обусловлена тем, что развитие многостаночной работы и совмещения процессий было и остается важным фактором повышения эффективности производства.
Многостаночное (многоагрегатное) обслуживание основано на использовании свободного машинного времени, в течении которого не требуется выполнять приемы ручной работы или наблюдать за ходом технологического процесса на данном станке, для обслуживания другого станка. В результате несколько станков работают параллельно или параллельно-последовательно и обслуживаются одним рабочим или бригадой, численность рабочих в которой меньше количества обслуживаемых ими станков.
Нормирование труда предполагает вариантность достижения цели производства, – создания товара или оказания услуг и удовлетворение спроса на них. Необходимый для предприятия результат производственной деятельности может быть достигнут на разном оборудовании, с использованием различных материалов, разным составом и содержанием технологических и трудовых процессов, различными инструментами и оснасткой, разными затратами топлива и энергии на технологические цели, разным уровнем затрат на заработную плату рабочих и управленческого персонала и т.д.
Задачи нормирования труда в том и заключаются, чтобы разработать варианты выполнения работ, определить допустимые варианты с учетом влияющих ограничений и выбрать из них или обосновать наиболее эффективный вариант. Реализация этой задачи требует управления нормированием труда в системе управления издержками производства. Управление издержками – это управление работниками, которые в свою очередь управляют средствами и предметами труда. Нормы труда выступают в качестве одного из средств управленческого воздействия на людей.
Нормирование труда – это вид деятельности по управлению производством, задачей которого является установление необходимых затрат и результатов труда, а также необходимых соотношений между численностью работников различных групп и количеством единиц оборудования.
Установление именно необходимых затрат, результатов и соотношений означает, что конкретные нормы труда должны соответствовать наиболее эффективным вариантам технологического процесса, организации труда и управления, т.е. способствовать наилучшему использованию трудовых и материальных ресурсов.[1]
Цель курсового проектирования - получить практические навыки в исследовании, проектировании и рационализации технологических и трудовых процессов рабочих, установлении норм труда, разработке рекомендаций и определении эффективности их внедрения.
Для достижения поставленной цели в работе необходимо решить следующие задачи: провести анализ организационно-технических параметров объекта (рабочего места); установить параметры исследуемого трудового процесса и время его выполнения; выявить недостатки существующего трудового процесса и в условиях его выполнения; спроектировать рациональный трудовой процесс с установлением необходимого времени его выполнения; рассчитать экономическую эффективность внедрения рационального трудового процесса.
1. Теоретические основы организации и нормирования труда многостаночников
1.1. Организация труда многостаночников
Под многостаночной работой понимают обслуживание одним или совместно несколькими рабочими (бригадой) двух и более машин. Рабочее место многостаночника представляет собой систему массового обслуживания, в которой машины являются источниками требований, а рабочие - каналами обслуживания.
Многостаночная работа может быть индивидуальной, когда один многостаночник работает на группе машин (одноканальная система), или групповой, когда несколько рабочих работает на группе машин, составляющих одно рабочее место (многоканальная система).[2]
Работа одного рабочего на нескольких машинах может быть представлена схематически следующим образом.
Пусть процесс на машинах № 1, 2, 3 (рис. 1) протекает так, что после 30 сек, затрачиваемых рабочим на выполнение определённого вида работ на одной машине (это время обозначим tз) следует 60 сек, в течении которых машина способна выпускать продукцию без участия работника. Это последнее время будем называть свободным машинным временем и обозначим tм.с. Примем также, что указанное чередование времени на выполнение рабочих приёмов работником и свободного машинного времени в дальнейшем повторяется строго в той же последовательности. Такой процесс называют циклическим. При заданных условиях рабочий, закончив выполнять рабочие приёмы на машине № 1, может перейти к машине № 2, а затем к № 3 и, затратив на них также по 30 сек, возвратиться к машине № 1 в тот момент, когда на ней закончится свободное машинное время. Те 60 сек, в течение которых каждая машина действует самостоятельно, рабочий может использовать на выполнение работы на двух других машинах.
Легко видеть, что при свободном машинном времени в 30 сек рабочему можно было бы поручить только две машины, а при 90 сек - четыре машины и т.д.
Рисунок 1 - Схема многостаночного обслуживания при одинаковых машинах
Таким образом, возможность многостаночной работы возникает в том случае, когда tм.с./ tз > 1.
Свободное машинное время представляет собой в основном ту часть машинного времени, которая не перекрывается временем занятости многостаночника на машине.
Время занятости многостаночника tз включает в себя перекрываемое и неперекрываемое время выполнения ручных приёмов, время на переходы от одной машины к другой, а также время, необходимое на активное наблюдение и отдых.
Многостаночная работа вызывает у рабочего связанные с передвижением дополнительные затраты времени. Организуя труд многостаночника, необходимо стремиться к сокращению этого времени. Увеличение доли свободного машинного времени в операционном цикле за счёт сокращения времени занятости рабочего позволяет расширить зону обслуживания многостаночника и повысить производительность его труда. Основными средствами достижения этой цели являются механизация ручных приёмов и совершенствование техники их выполнения.
В рассмотренном выше примере занятость рабочего и свободное машинное время приняты одинаковыми на всех машинах. Это условие легче осуществить при обслуживании однотипных машин и выработке на них одинаковой продукции.
Когда применяют разнотипное оборудование и вырабатывают различную продукцию, длительность занятости рабочего, как правило, разная. Однако и в этом случае при определённых условиях возможна строго циклическая работа.
Так, на рис. 2 представлен график многостаночной работы при длительности обслуживания на машине № 1 30 сек и свободном машинном времени 60 сек. Следовательно, длительность цикла равна 90 сек. На машине № 2 занятость рабочего принята 40 сек, в таком случае рабочий вернётся своевременно к машине № 1, если будет выполнять работу на машине № 3 20 сек. Продолжительность оперативного цикла на всех машинах должна быть равна сумме затрат времени рабочего на всех обслуживаемых машинах, следовательно цикл должен быть одинаковой длительности на всех машинах. Кроме того, свободное машинное время на каждой из машин равно сумме затрат времени рабочего на всех других машинах. На рис. 3 свободное машинное время на машине №1составляет 60сек, а следовательно, длительность занятости рабочего на машинах № 2 и № 3 также 40 + 20 = 60 сек; соответственно на второй tм.с = 30 + 20 = 50 сек, а на третьей tм.с = 30 + 40 = 70 сек. Длительность цикла на всех машинах будет tц = 30 + 60 = 40 + 50 = 20 + 70 = 90 сек.
Рисунок 2 - Схема многостаночного обслуживания при различных машинах
Из приведённых примеров легко установить, что многостаночная работа без каких либо дополнительных потерь, связанных с работой рабочего на нескольких машинах, предполагает ряд определённых условий. [3]
Многостаночник не может непрерывно следить за действием всех машин, поэтому они должны быть оснащены различными приспособлениями, которые предупреждали бы наработку брака продукции, разладку или поломку отдельных механизмов.
Строго согласованное чередование работ, выполняемых рабочим на нескольких машинах, требует вполне определённых соотношений между временем занятости и свободным машинным временем. Схема многостаночной работы, приведённая на рис. 1, предполагает кратность этих величин, а схема, приведённая на рис. 2 . равенство суммы длительностей занятости рабочего на любых двух машинах и свободного машинного времени работы третьей машины. В обоих случаях продолжительность цикла на всех машинах, на которых трудится рабочий, должна быть одинаковой.
Однажды установленные отношения между временем занятости и свободным машинным временем, а также характер чередования этого времени должны сохраняться в неизменном виде. Установить и поддерживать такие условия на производстве представляет значительные трудности.
Даже такую простую схему многостаночной работы, как приведённая на рис. 1, можно осуществить только в массовом производстве с однотипным оборудованием и неизменными в течение длительного времени операциями.
Нарушение рассмотренных условий приводит к специфическим для многостаночной работы потерям времени. Пусть, как и в первом примере, длительность занятости рабочего на одной машине составляет 30 сек, длительность же цикла примем 80 сек, следовательно, свободное машинное время будет составлять 50 сек (рис.3). Поскольку на выполнение трудовых приёмов на двух машинах многостаночнику потребуется 60 сек, то очевидно, что в каждом цикле будет дополнительный простой машин продолжительностью 10 сек из-за запаздывания работника, в виду занятости на других машинах.[4]
Простои машин в ожидании многостаночника, занятого работой на других машинах или передвижением к ожидающей его машине, называют перерывами из-за совпадения
Рисунок 3 – Простои при многостаночной работе
Из рис. 3 видно, что перерывов из-за совпадения можно избежать, если поручить рабочему работать на двух машинах, однако в этом случае не будет полностью использовано рабочее время многостаночника.
Таким образом, даже при строго регламентированном равномерном технологическом процессе многостаночная работа без потерь возможна только при определённых условиях. Их соблюдение практически возможно при работе многостаночника на сравнительно небольшом количестве машин. Чем больше машин у многостаночника, тем вероятность отклонений от указанных строгих соотношений возрастает. Действительно, работа на большом количестве машин предполагает, что время их действия без рабочего во много раз превышает затраты времени рабочего на каждую машину. При этом даже небольшое колебание, например в скоростном режиме работы оборудования, может изменить машинное время за длительный промежуток времени на величину большую, чем время занятости рабочего на одной машине. В ещё большей степени будут влиять колебания ручного времени, длительность которого зависит от характера рабочих приёмов и темпа их выполнения. Возможны и отдельные случайные перерывы в работе машин. [5]
Борьба с нецикличностью технологического процесса и в связи с этим с неравномерной загрузкой многостаночников, а также с возникающими в результате этого производственными потерями является важнейшей задачей организации многостаночной работы. В этих условиях нельзя полностью устранить потери времени, но сократить их до минимума вполне возможно.
1.2. Нормирование труда многостаночников
Нормы труда устанавливают многостаночнику в виде норм выработки, норм обслуживания и норм производительности машин.
Норма выработки - это количество единиц продукции, устанавливаемое к выработке рабочему в единицу времени при определённых организационно-технических условиях работы.
Норма обслуживания - это количество единиц оборудования, устанавливаемое для одновременного обслуживания рабочему при определённых организационно-технических условиях работы.
Норма производительности оборудования - это количество единиц продукции, устанавливаемое к выработке на одной единице оборудования в единицу времени при определённых организационно-технических условиях работы. [6]
Норму выработки многостаночнику устанавливают в зависимости от нормы производительности машины и нормы обслуживания
Нв = Нп · Но (1.1)
где Нв - норма выработки многостаночника за час;
Нп - норма производительности машины за час;
Но - норма обслуживания.
При равномерном технологическом процессе, когда не возникает перерывов из-за совпадения, норма производительности машины не зависит от нормы обслуживания многостаночника и её рассчитывают так же, как и при работе рабочего на одной машине. В условиях неравномерного процесса норму производительности машин, обслуживаемых многостаночником, следует определять с учётом перерывов из-за совпадения по формуле:
Нп = (Тсм - Тб) / (tм + tвн + tс) (1.2)
где Нп - норма производительности машины за смену;
Тсм - продолжительность смены;
Тб - неперекрываемое время обслуживания рабочего места за смену, включая время на отдых и личные надобности;
tм - основное машинное время на единицу продукции (машинным временем называют время в течение которого единица оборудования, работая, выполняет операцию над единицей изделия).
tвн - неперекрываемое вспомогательное время на единицу продукции;
tс - перерывы из-за совпадения на единицу продукции.
Кроме формулы (1) норму производительности машин можно определить и по формуле:
Нп = А · Кп.в. (1.3)
где Нп - норма производительности машины;
А - теоретическая производительность машины;
Кп.в. - коэффициент полезного времени.
Теоретическая производительность машины это количество единиц продукции, которое машина могла бы выработать при непрерывной машинной работе в единицу времени, т.е. если бы не было никаких перерывов в технологическом процессе.
А = Тсм / tм (1.4)
Коэффициент полезного времени показывает долю основного времени в норме времени, т.е. ту часть времени в течение которого машина производит продукт.
Коэффициент полезного времени может быть найден путём деления нормы производительности машины на теоретическую производительность.
Кп.в. = Нп / А (1.5)
Подставив в формулу (1.5) соответствующие значения из формул (1.2) и (1,3) получим выражение для определения коэффициента полезного времени:
Кп.в. = [(Тсм . Тб) / (tм + tвн + tс)] : (Тсм / tм ) =
= [(Тсм - Тб) tм ] / [(tм + tвн + tс) Тсм] (1.6)
обозначим
tм / (tм + tвн + tс) = Ка (1.7)
(Тсм . Тб) / Тсм = Кб (1.8)
отсюда Кп.в. = Ка Кб (1.9)
где Ка . коэффициент, учитывающий простои по группе «а», т.е. простои, связанные с поддержанием технологического процесса;
Кб - коэффициент, учитывающий простои машин группы «б», т.е. простои, связанные с обслуживанием рабочего места, а также отдыхом и личными надобностями.
Многостаночное обслуживание требует организации рабочего места многостаночника, при которой его затраты труда на выполнение работы, а также на переходы от машины к машине являются минимальными. Здесь имеются в виду соответствующее расположение машин и другого оборудования на рабочем месте, выбор наивыгоднейшего маршрута рабочего, передачи части работ обслуживающему персоналу (например, чистки и смазки машины, наладки оборудования и т.п.). Все эти мероприятия позволяют увеличить число машин, на которых работает основной рабочий.[7]
Многостаночное обслуживание возможно в тех случаях, когда соблюдается условие:
tм.с./ tз > 1 (1.10)
где tм.с. - машинное свободное время (время работы машины без участия многостаночника) при выработке единицы продукции;
tз - время занятости многостаночника при выработке единицы изделия на одной машине.
Число машин, на которых может работать многостаночник, находится, естественно, в определённых пределах. С ростом числа машин - производительность рабочего повысится, но производительность оборудования при этом будет уменьшаться, в связи с увеличением его остановов из-за совпадения. Подобная зависимость имеет место до определённого предела, выше которого рост производительности труда многостаночника прекратится: уменьшение производительности оборудования из-за совпадений не будет компенсироваться увеличением числа машин, на которых работает многостаночник.
При уменьшении числа машин, находящихся в ведении многостаночника, производительность оборудования повышается в связи с сокращением перерывов в работе оборудования из-за совпадения, но у рабочего возникают простои, вызванные недогрузкой.
И потери времени работы оборудования из-за совпадения, и простои многостаночника из-за его недогрузки будут влиять на себестоимость продукции.
Норму обслуживания устанавливают с учётом организационно-технических условий производства. Так, в некоторых случаях (например, при наличии «узких мест» в производстве), целесообразно предусматривать пониженные нормы обслуживания оборудования с некоторым ущербом для производительности труда на данном участке. А, предположим, при недостатке рабочих уместно, чтобы предотвратить простои оборудования по этой причине, устанавливать с некоторым ущербом для производительности оборудования повышенные нормы обслуживания. Одним словом, в зависимости от конкретных условий норму обслуживания приходится выбирать после определения её расчётной величины. [8]
В самом простом случае, когда технологический процесс протекает без каких либо потерь времени, а также производится однородная продукция на однотипном оборудовании, норму обслуживания можно рассчитать по формуле
nрасч = tц / tз (1.11)
В тоже время,
tц = tз + tм.с (1.12)
Однако время занятости работника может складываться из вспомогательного перекрываемого времени и вспомогательного неперекрываемого времени, т.е.
tз = tв.н. + tв.п., где tв.н. (1.13)
вспомогательное неперекрываемое время выполнения ручных рабочих приёмов; tв.п. - вспомогательное перекрываемое время выполнения ручных рабочих приёмов. Другими словами,
tц = tв.н. + tв.п. + tм.с (1.14)
Тогда, время цикла графически можно изобразить так, как это показано на рис. 4. Поскольку в течении перекрываемого времени машина работает и выпускает продукцию, то оно входит в машинное время, т.е., в данном случае машинное время состоит из перекрываемого времени выполнения ручных приёмов и машинного свободного времени tм = tв.п. + tм.с, таким образом можно записать tц = tм + tв.н.. Тогда, согласно формуле (1.11)
nрасч = (tм + tв.н ) / tз (1.15)
Для неравномерного нецикличного технологического процесса, где, как известно, происходят потери времени как у оборудования из-за совпадения, так и у работника из-за различных микропауз, возникающих в работе, число машин, которые сможет обслужить многостаночник, определяют с учётом потерь времени из-за совпадения и возникающих микропауз по формуле:
nрасч = [(tм + tв.н ) / tз ] Кс Кд (1.16)
где Кс . коэффициент совпадений, учитывающий время перерывов из-за совпадений;
Кд - коэффициент учитывающий потери времени у рабочего за счёт возникновения микропауз в процессе работы многостаночника.
Рисунок 5 – Неравномерный технологический процесс
В расчётах часто вместо времени занятости рабочего (tз ) используют коэффициент загруженности работой. Коэффициент загруженности работой (Кз.р.) показывает долю времени, затрачиваемого многостаночником на полезную работу, т.е. на выполнение рабочих приёмов и активное наблюдение.
Кз.р. = tз.р / tз (1.17)
где tз.р . время занятости (загруженности) рабочего выполнением рабочих приёмов на единицу продукции, без учёта времени на перерывы, переходы и пассивное наблюдение. Согласно формуле (1. 17) можно записать:
tз= tз.р / Кз.р. (1.18)
Подставив значение tз из формулы (18) в формулу (16) получим:
nрасч = [(tм + tв.н ) / tз ] Кс Кд Кз.р (1.19)
Именно по этой формуле и определяют норму обслуживания для большинства многостаночников.
Кз.р устанавливают по данным наблюдений, дифференцированно, с учётом метода обслуживания рабочим оборудования (маршрутный, сторожевой, комбинированный и т.д.)[9]
Коэффициент Кд также устанавливают по данным наблюдений. Величина этого коэффициента находится в пределах 0,9 - 0,97. Нижний предел этого коэффициента относится к варианту обслуживания оборудования, вырабатывающего неоднородную продукцию, а верхний -к варианту обслуживания оборудования, вырабатывающего однородную продукцию. Коэффициент совпадений Кс определяется по таблицам, в которых величина его дифференцирована в зависимости от зоны обслуживания и коэффициента занятости рабочего на одном станке. Если характер выполняемой работы многостаночника не связан с выработкой определённых единиц продукции, то затраты времени рабочего необходимо рассчитывать за смену и расчётную зону обслуживания определять по формуле:
nрасч =[(Тсм - Тб) / Тз] Кс Кд (1. 20)
где Тз - время занятости многостаночника на одной машине в течение смены.
А в тех случаях, когда работа многостаночника не связана с выработкой определённых единиц продукции и, к тому же, уходя с рабочего места на отдых или по естественным надобностям, он не останавливает оборудование, то расчётную зону обслуживания определяют по формуле:
nрасч =(Тсм / Тз) Кс Кд (1.21)
2. Проектирование норм труда при многостаночной работе
2.1. Установление необходимого числа станков в условиях одностаночного обслуживания
Исходные данные:
Перечень и количество изготавливаемых на участке деталей, их масса, а также данные об основном и вспомогательном времени по каждой детали представлены в таблице 1. Согласно варианту исключим из расчетов номера детале-операций 7,5,6.
Таблица 1
Исходные данные для расчета норм труда
№ детале-операций |
Основное время, мин. |
Вспомогательное время, мин. |
Масса детали, кг |
Программа на месяц, шт. |
|
перекрываемое |
неперекрываемое |
||||
1 |
5,0 |
0,25 |
1,0 |
8 |
500 |
2 |
3,0 |
0,15 |
0,5 |
9 |
100 |
3 |
2,5 |
0,3 |
0,5 |
12 |
200 |
4 |
6,5 |
0,15 |
0,7 |
11 |
500 |
8 |
8,3 |
0,65 |
0,8 |
8 |
200 |
9 |
4,4 |
0,2 |
0,8 |
7 |
300 |
10 |
5,4 |
0,2 |
0,8 |
7 |
300 |
11 |
1,3 |
0,35 |
0,4 |
5 |
500 |
12 |
7,4 |
0,25 |
0,5 |
11 |
100 |
13 |
2,5 |
0,2 |
0,2 |
14 |
100 |
14 |
6,0 |
0,3 |
0,3 |
15 |
100 |
15 |
8,1 |
0,4 |
0,5 |
16 |
100 |
16 |
1,2 |
0,3 |
0,25 |
4 |
100 |
17 |
3,2 |
0,1 |
0,4 |
5 |
500 |
18 |
5,0 |
0,2 |
0,6 |
19 |
1000 |
19 |
4,1 |
0,2 |
0,7 |
18 |
150 |
20 |
3,5 |
0,1 |
0,4 |
17 |
200 |
21 |
5,5 |
0,3 |
1,5 |
15 |
600 |
22 |
9,1 |
0,5 |
0,38 |
12 |
700 |
23 |
8,4 |
0,6 |
0,4 |
14 |
600 |
24 |
3,3 |
0,8 |
0,5 |
10 |
150 |
25 |
1,8 |
0,6 |
0,3 |
8 |
250 |
26 |
2,7 |
0,8 |
0,25 |
9 |
180 |
27 |
4,9 |
0,9 |
0,6 |
17 |
1100 |
28 |
6,7 |
0,7 |
0,2 |
5 |
1000 |
29 |
7,6 |
0,3 |
0,7 |
7 |
900 |
30 |
10,0 |
0,2 |
0,6 |
10 |
400 |
Значение необходимого числа станков для выполнения производственной программы в условиях одностаночного обслуживания (Nн) определяется по формуле (2.1.):
(2.1.)
где: ТТ – технологическая трудоемкость изготовления деталей на участке за месяц, мин;
F1 – полезный фонд времени работы одного станка за месяц, мин;
Тштi – норма штучного времени на выполнение i-ой детале-операции в условиях одностаночного обслуживания, мин;
Рi – месячная программа по операциям (i = 1, 2, ..., к), шт;
Д – количество рабочих дней в месяце, дн;
Тсм – длительность времени смены, мин;
Ксм – коэффициент сменности работы на участке.
Норма штучного времени выполнения одной детале-операции при работе на одном станке в условиях серийного производства (Тштi) определяется по формуле:
(2.2)
где: Топ – оперативное время выполнения детале-операций, мин;
Коб – время на техническое и организационное обслуживание рабочего места, % от оперативного времени (при одностаночном обслуживании оно колеблется в пределах от 3,5 до 5,5 % оперативного времени);
Котл – время на отдых и личные надобности для рабочего (выбираем по таблице 2), % от оперативного времени.
Таблица 2
Время на отдых и личные надобности для рабочего
(способ установки детали вручную)
Масса детали, кг |
Время на отдых и личные надобности, % от оперативного времени |
до 10 |
2,0 |
свыше 10 |
4,0 |
Оперативное время выполнения детале-операции (Топi) определяется по формуле:
(2.3)
где: Тоi – основное машинное время i-ой операции, мин;
Твнi – вспомогательное время выполнения i-ой операции, неперекрываемое основным машинным временем, мин.
Данные для расчета необходимого числа станков приведены в таблице 3.
Таблица 3
Расчет норм штучного времени и технологической трудоемкости
изготовления деталей за месяц на участке в условиях одностаночного обслуживания
№ детали |
Топ, мин |
Коб, (4% от Топ) |
Котл, (2% от Топ) |
|
Тшт, мин |
Р, шт |
|
1 |
6 |
4.0 |
2 |
1,06 |
6,36 |
500 |
3180 |
2 |
3,5 |
2 |
1,06 |
3,71 |
100 |
371 |
|
3 |
3 |
4 |
1,08 |
3,24 |
200 |
648 |
|
4 |
7,2 |
4 |
1,08 |
7,776 |
500 |
3888 |
|
8 |
9,1 |
2 |
1,06 |
9,646 |
200 |
1929,2 |
|
9 |
5,2 |
2 |
1,06 |
5,512 |
300 |
1653,6 |
|
10 |
6,2 |
2 |
1,06 |
6,572 |
300 |
1971,6 |
|
11 |
1,7 |
2 |
1,06 |
1,802 |
500 |
901 |
|
12 |
7,9 |
4 |
1,08 |
8,532 |
100 |
853,2 |
|
13 |
2,7 |
4 |
1,08 |
2,916 |
100 |
291,6 |
|
14 |
6,3 |
4 |
1,08 |
6,804 |
100 |
680,4 |
|
15 |
8,6 |
4 |
1,08 |
9,288 |
100 |
928,8 |
|
16 |
1,45 |
2 |
1,06 |
1,537 |
100 |
153,7 |
|
17 |
3,6 |
2 |
1,06 |
3,816 |
500 |
1908 |
|
18 |
5,6 |
4 |
1,08 |
6,048 |
1000 |
6048 |
|
19 |
4,8 |
4 |
1,08 |
5,184 |
150 |
777,6 |
|
20 |
3,9 |
4 |
1,08 |
4,212 |
200 |
842,4 |
|
21 |
7 |
4 |
1,08 |
7,56 |
600 |
4536 |
|
22 |
9,48 |
4 |
1,08 |
10,2384 |
700 |
7166,88 |
|
23 |
8,8 |
4 |
1,08 |
9,504 |
600 |
5702,4 |
|
24 |
3,8 |
4 |
1,08 |
4,104 |
150 |
615,6 |
|
25 |
2,1 |
2 |
1,04 |
2,184 |
250 |
546 |
|
26 |
2,95 |
2 |
1,04 |
3,068 |
180 |
552,24 |
|
27 |
5,5 |
4 |
1,08 |
5,94 |
1100 |
6534 |
|
28 |
6,9 |
2 |
1,04 |
7,176 |
1000 |
7176 |
|
29 |
8,3 |
2 |
1,04 |
8,632 |
900 |
7768,8 |
|
30 |
10,6 |
4 |
1,08 |
11,448 |
400 |
4579,2 |
|
Итого: |
72203,22 |
По полученным итоговым данным устанавливаем необходимое расчетное число станков для выполнения всей производственной программы (результат расчета округляем до целого числа в большую сторону):
(шт.)
При этом количество станков определяет и необходимое количество рабочих-станочников.
2.2. Анализ возможности организации многостаночного обслуживания на участке
Для этого сначала устанавливаются основные составные части времени занятости рабочих и времени работы оборудования в расчете на одну деталь и на месячную программу.
Время занятости рабочего по операциям (Тзi) определяется по формуле:
(2.5)
где: Твнi – вспомогательное неперекрываемое время на выполнение i-ой операции, мин;
Твпi – вспомогательное перекрываемое время на выполнение i-ой операции, мин;
Танi – время активного наблюдения за работой оборудования при выполнении i-ой операции (составляет 5 % от основного времени операции), мин;
Тпi – время на переход от одного станка к другому (средняя величина составляет 0,015 мин на м, в расчетах время на один переход принимаем равным 0,05 мин).
Машинно-свободное время для рабочего при выполнении любой операции (Тмсi) определяется по формуле:
(2.6)
где: Тоi – основное машинное время i-ой операции, мин.
Результаты расчетов представлены в таблице 4.
Таблица 4
Расчет основных частей времени занятости рабочих и времени работы оборудования (на одну деталь; на месячную программу)
№ детали |
На одну деталь |
На месячную программу |
||||||||||||||
То |
Твп |
Твн |
Тан (5% от То) |
Тп |
Тз |
Тмс |
Топ |
Р |
Тмс |
Тз |
Топ |
|||||
1 |
2 |
3 |
4 |
5 |
6 |
7 |
8 |
9 |
10 |
11 |
12 |
13 |
||||
1 |
5,0 |
0,25 |
1,0 |
0,25 |
0,05 |
1,5 |
4,45 |
6 |
500 |
2225 |
750 |
3000 |
||||
2 |
3,0 |
0,15 |
0,5 |
0,15 |
0,85 |
2,65 |
3,5 |
100 |
265 |
85 |
350 |
|||||
3 |
2,5 |
0,3 |
0,5 |
0,125 |
0,975 |
2,025 |
3 |
200 |
405 |
195 |
600 |
|||||
4 |
6,5 |
0,15 |
0,7 |
0,325 |
1,225 |
5,975 |
7,2 |
500 |
2987,5 |
612,5 |
3600 |
|||||
8 |
8,3 |
0,65 |
0,8 |
0,415 |
1,915 |
7,185 |
9,1 |
200 |
1437 |
383 |
1820 |
|||||
9 |
4,4 |
0,2 |
0,8 |
0,22 |
1,27 |
3,93 |
5,2 |
300 |
1179 |
381 |
1560 |
|||||
10 |
5,4 |
0,2 |
0,8 |
0,27 |
1,32 |
4,88 |
6,2 |
300 |
1464 |
396 |
1860 |
|||||
11 |
1,3 |
0,35 |
0,4 |
0,065 |
0,865 |
0,835 |
1,7 |
500 |
417,5 |
432,5 |
850 |
|||||
12 |
7,4 |
0,25 |
0,5 |
0,37 |
1,17 |
6,73 |
7,9 |
100 |
673 |
117 |
790 |
|||||
13 |
2,5 |
0,2 |
0,2 |
0,125 |
0,575 |
2,125 |
2,7 |
100 |
212,5 |
57,5 |
270 |
|||||
14 |
6,0 |
0,3 |
0,3 |
0,3 |
0,95 |
5,35 |
6,3 |
100 |
535 |
95 |
630 |
|||||
15 |
8,1 |
0,4 |
0,5 |
0,405 |
1,355 |
7,245 |
8,6 |
100 |
724,5 |
135,5 |
860 |
|||||
16 |
1,2 |
0,3 |
0,25 |
0,06 |
0,66 |
0,79 |
1,45 |
100 |
79 |
66 |
145 |
|||||
17 |
3,2 |
0,1 |
0,4 |
0,16 |
0,71 |
2,89 |
3,6 |
500 |
1445 |
355 |
1800 |
|||||
18 |
5,0 |
0,2 |
0,6 |
0,25 |
1,1 |
4,5 |
5,6 |
1000 |
4500 |
1100 |
5600 |
|||||
19 |
4,1 |
0,2 |
0,7 |
0,205 |
1,155 |
3,645 |
4,8 |
150 |
546,75 |
173,25 |
720 |
|||||
20 |
3,5 |
0,1 |
0,4 |
0,175 |
0,725 |
3,175 |
3,9 |
200 |
635 |
145 |
780 |
|||||
21 |
5,5 |
0,3 |
1,5 |
0,275 |
2,125 |
4,875 |
7 |
600 |
2925 |
1275 |
4200 |
|||||
22 |
9,1 |
0,5 |
0,38 |
0,455 |
0,05 |
1,385 |
8,095 |
9,48 |
700 |
5666,5 |
969,5 |
6636 |
||||
23 |
8,4 |
0,6 |
0,4 |
0,42 |
1,47 |
7,33 |
8,8 |
600 |
4398 |
882 |
5280 |
|||||
24 |
3,3 |
0,8 |
0,5 |
0,165 |
1,515 |
2,285 |
3,8 |
150 |
342,75 |
227,25 |
570 |
|||||
25 |
1,8 |
0,6 |
0,3 |
0,09 |
1,04 |
1,06 |
2,1 |
250 |
265 |
260 |
525 |
|||||
26 |
2,7 |
0,8 |
0,25 |
0,135 |
1,235 |
1,715 |
2,95 |
180 |
308,7 |
222,3 |
531 |
|||||
27 |
4,9 |
0,9 |
0,6 |
0,245 |
1,795 |
3,705 |
5,5 |
1100 |
4075,5 |
1974,5 |
6050 |
|||||
28 |
6,7 |
0,7 |
0,2 |
0,335 |
1,285 |
5,615 |
6,9 |
1000 |
5615 |
1285 |
6900 |
|||||
29 |
7,6 |
0,3 |
0,7 |
0,38 |
1,43 |
6,87 |
8,3 |
900 |
6183 |
1287 |
7470 |
|||||
30 |
10,0 |
0,2 |
0,6 |
0,5 |
1,35 |
9,25 |
10,6 |
400 |
3700 |
540 |
4240 |
|||||
Итого: |
53210,2 |
14401,8 |
67637 |
|
||||||||||||
По результатам расчетов определим возможность организации многостаночного обслуживания на участке. Для этого по данным таблицы 4 установим соотношение между временем занятости и оперативным временем, исходя из норм, рассчитанных для каждой операции. Расчеты представлены в таблице 5.
Таблица 5.
Расчет соотношения между временем занятости и оперативным временем
№ детали |
Тз |
Топ |
Тз / Топ |
1 |
750 |
3000 |
0,25 |
2 |
85 |
350 |
0,24285714 |
3 |
195 |
600 |
0,325 |
4 |
612,5 |
3600 |
0,17013889 |
8 |
383 |
1820 |
0,21043956 |
9 |
381 |
1560 |
0,24423077 |
10 |
396 |
1860 |
0,21290323 |
11 |
432,5 |
850 |
0,50882353 |
12 |
117 |
790 |
0,14810127 |
13 |
57,5 |
270 |
0,21296296 |
14 |
95 |
630 |
0,15079365 |
15 |
135,5 |
860 |
0,15755814 |
16 |
66 |
145 |
0,45517241 |
17 |
355 |
1800 |
0,19722222 |
18 |
1100 |
5600 |
0,19642857 |
19 |
173,25 |
720 |
0,240625 |
20 |
145 |
780 |
0,18589744 |
21 |
1275 |
4200 |
0,30357143 |
22 |
969,5 |
6636 |
0,14609705 |
23 |
882 |
5280 |
0,16704545 |
24 |
227,25 |
570 |
0,39868421 |
25 |
260 |
525 |
0,4952381 |
26 |
222,3 |
531 |
0,41864407 |
27 |
1974,5 |
6050 |
0,32636364 |
28 |
1285 |
6900 |
0,18623188 |
29 |
1287 |
7470 |
0,17228916 |
30 |
540 |
4240 |
0,12735849 |
На участках с переменной номенклатурой обрабатываемых деталей определим среднее значение показателя занятости рабочих (Кз):
(2.7)
где: Тзi – время занятости рабочего по операциям, выполняемым на данном участке, мин; Топi – оперативное время по операциям, выполняемым на данном участке, мин; Рi – месячная программа изготовления деталей на участке, шт.
Среднее значение показателя занятости рабочих равно:
Коэффициент занятости меньше 1, следовательно, организация многостаночного обслуживания на участке возможна.
Таким образом, из расчетов видно, что введение на участке многостаночного обслуживания не только возможно, но и целесообразно.
Большое значение для рациональной организации многостаночного обслуживания имеет правильно установленная норма обслуживания, которая является основной для оптимальной расстановки рабочих, нормирования работ и организации оплаты труда многостаночников.
В условиях серийного производства норма обслуживания станков одним рабочим (Ноб) определяется по формуле:
(2.8)
Данные для расчета нормы обслуживания берутся из таблицы 4 (результат расчета округляем до целого числа в меньшую сторону):
Определим необходимое число станков для выполнения производственной программы в условиях многостаночного обслуживания (Nн.м) по формуле:
(2.9)
Результат расчета округляем до целого числа в большую сторону:
(шт.)
С учетом принятой нормы обслуживания выбираем группу станков, на которых целесообразно внедрить многостаночное обслуживание (Nм). При этом число станков должно быть не меньше необходимого числа станков для выполнения производственной программы в условиях многостаночной работы (5 станков) и не больше необходимого числа станков для выполнения производственной программы в условиях одностаночного обслуживания (7 станков).
Таким образом, 5 ≤ Nм = 6 ≤ 7
Принимаем Nм = 6 шт.
Определим численность рабочих-многостаночников (Нч) по формуле:
(чел.)
Рассчитаем для каждой операции норму штучного времени при многостаночной работе (Тшт.мi) по формуле:
где: Атех – время на техническое обслуживание рабочего места, % от оперативного времени;
Аорг – время на организационное обслуживание рабочего места, % от оперативного времени;
Аотл – время на отдых и личные надобности рабочему, % от оперативного времени (в условиях многостаночного обслуживания время на отдых и личные надобности определяется в том же порядке, как и при работе на одном станке, т.е. Аотл = Котл);
Кс – коэффициент учитывающий совпадение окончания машинной работы на одном станке со временем занятости рабочего на других станках.
Величина коэффициента совпадения (Кс) определяется по таблице 6 в зависимости от числа обслуживаемых станков и величины коэффициента занятости рабочего при выполнении i-ой детале-операции.
Таблица 6
Определение коэффициента совпадения обслуживания станков для одного рабочего (Кс)
Количество обслуживаемых станков |
Коэффициент занятости рабочего при выполнении операции Кз, до |
||||||||
0,10 |
0,15 |
0,20 |
0,25 |
0,30 |
0,35 |
0,40 |
0,45 |
0,50 |
|
1 |
2 |
3 |
4 |
5 |
6 |
7 |
8 |
9 |
10 |
2 |
1,01 |
1,02 |
1,04 |
1,06 |
1,09 |
1,12 |
1,16 |
1,20 |
1,25 |
3 |
1,01 |
1,02 |
1,05 |
1,09 |
1,15 |
1,22 |
1,29 |
1,39 |
1,49 |
4 |
1,04 |
1,09 |
1,16 |
1,26 |
1,38 |
1,52 |
1,68 |
1,85 |
2,03 |
5 |
1,05 |
1,13 |
1,25 |
1,40 |
1,59 |
1,80 |
2,03 |
2,27 |
2,51 |
6 |
1,07 |
1,19 |
1,36 |
1,58 |
1,84 |
2,12 |
2,41 |
2,70 |
- |
7 |
1,10 |
1,26 |
1,49 |
1,79 |
2,12 |
2,45 |
2,80 |
- |
- |
8 |
1,13 |
1,34 |
1,65 |
2,02 |
2,41 |
2,80 |
- |
- |
- |
Коэффициент занятости определяется по формуле:
Оперативное время выполнения i-ой детале-операции определяется по формуле:
Время на техническое обслуживание рабочего места в условиях многостаночной работы определяется по формуле:
где: Ктех – время на техническое обслуживание рабочего места при одностаночном обслуживании, % от оперативного времени (при одностаночном обслуживании это время колеблется в пределах от 2 до 3 % оперативного времени).
Время на организационное обслуживание рабочего места в условиях многостаночной работы определяется по формуле:
где: Корг – время на организационное обслуживание рабочего места при одностаночном обслуживании, % от оперативного времени (при одностаночном обслуживании это время колеблется в пределах от 1,5 до 2,5 % оперативного времени).
Расчет норм штучного времени представлен в таблице 7.
Таблица 7
Расчет норм времени детале-операций для условий многостаночного обслуживания
№ детали |
Топ, мин |
Атех, % |
Аорг, % |
Аотл, % |
|
Кз |
Кс |
|
Тшт.м, мин |
1 |
2 |
3 |
4 |
5 |
6 |
7 |
8 |
9 |
10 |
1 |
6 |
10,0 |
8,0 |
2 |
1,2 |
0,25 |
1,79 |
0,451261 |
3,249079 |
2 |
3,5 |
2 |
1,2 |
0,24 |
1,79 |
0,434714 |
1,825799 |
||
3 |
3 |
4 |
1,22 |
0,32 |
2,45 |
0,79625 |
2,914275 |
||
4 |
7,2 |
4 |
1,22 |
0,17 |
1,49 |
0,253507 |
2,226805 |
||
8 |
9,1 |
2 |
1,2 |
0,21 |
1,79 |
0,376687 |
4,113422 |
||
9 |
5,2 |
2 |
1,2 |
0,24 |
1,79 |
0,437173 |
2,72796 |
||
10 |
6,2 |
2 |
1,2 |
0,21 |
1,79 |
0,381097 |
2,835362 |
||
11 |
1,7 |
2 |
1,2 |
0,51 |
2,51 |
1,277147 |
2,60538 |
||
12 |
7,9 |
4 |
1,22 |
0,15 |
1,26 |
0,186608 |
1,798528 |
||
13 |
2,7 |
4 |
1,22 |
0,21 |
1,79 |
0,381204 |
1,255686 |
||
14 |
6,3 |
4 |
1,22 |
0,15 |
1,26 |
0,19 |
1,46034 |
||
15 |
8,6 |
4 |
1,22 |
0,16 |
1,26 |
0,198523 |
2,082903 |
||
16 |
1,45 |
2 |
1,2 |
0,46 |
2,51 |
1,142483 |
1,98792 |
||
17 |
3,6 |
2 |
1,2 |
0,19 |
1,49 |
0,293861 |
1,26948 |
||
18 |
5,6 |
4 |
1,22 |
0,19 |
1,49 |
0,292679 |
1,999583 |
||
19 |
4,8 |
4 |
1,22 |
0,24 |
1,79 |
0,430719 |
2,52229 |
||
20 |
3,9 |
4 |
1,22 |
0,18 |
1,26 |
0,234231 |
1,114471 |
||
21 |
7 |
4 |
1,22 |
0,30 |
2,12 |
0,643571 |
5,496096 |
||
22 |
9,48 |
4 |
1,22 |
0,15 |
1,26 |
0,184082 |
2,129019 |
||
23 |
8,8 |
4 |
1,22 |
0,17 |
1,26 |
0,210477 |
2,259681 |
||
24 |
3,8 |
4 |
1,22 |
0,39 |
2,8 |
1,116316 |
5,175241 |
||
25 |
2,1 |
2 |
1,2 |
0,49 |
2,51 |
1,243048 |
3,132481 |
||
26 |
2,95 |
2 |
1,2 |
0,42 |
2,7 |
1,130339 |
4,0014 |
||
27 |
5,5 |
4 |
1,22 |
0,33 |
2,45 |
0,799591 |
5,365256 |
||
28 |
6,9 |
2 |
1,2 |
0,18 |
1,49 |
0,277486 |
2,297584 |
||
29 |
8,3 |
2 |
1,2 |
0,17 |
1,49 |
0,256711 |
2,556842 |
||
30 |
10,6 |
4 |
1,22 |
0,13 |
1,26 |
0,160472 |
2,075224 |
В соответствии с принятой нормой обслуживания спроектируем график многостаночного обслуживания. Для этого составим перечень детале-операций, которые будут выполняться на этих станках: 1, 8, 20, 30. Для построения графика используем данные о времени занятости рабочего и машинно-свободного времени по выбранным деталям, которые представлены в таблице 8.
Таблица 8
Данные о времени занятости рабочего и машинно-свободного времени по выбранным деталям
№ детали |
Тз, мин |
Тмс, мин |
Топ, мин |
1 |
1,55 |
4,45 |
6,0 |
8 |
1,915 |
7,185 |
9,1 |
20 |
0,725 |
3,175 |
3,9 |
30 |
1,35 |
9,25 |
10,6 |
Итого: |
5,54 |
24,06 |
29,6 |
На основе графика определим: продолжительность цикла многостаночного обслуживания – 10,6 мин; величина свободного времени рабочего в течение одного цикла – 5,06 мин; время простоев оборудования в течение одного цикла –12,8 мин.
Правильность построения графика и сделанных выводов проверим аналитическим способом.
Определим длительность цикла многостаночной работы (Тц). Так как наибольшее машинно-свободное время больше суммарной занятости рабочего на остальных станках, то длительность цикла определяется детале-операцией с наибольшим оперативным временем (Топб):
(2.10)
мин.
Определим свободное время рабочего в цикле многостаночного обслуживания (Тсв) по формуле:
(2.11)
мин.
|
|
|










|



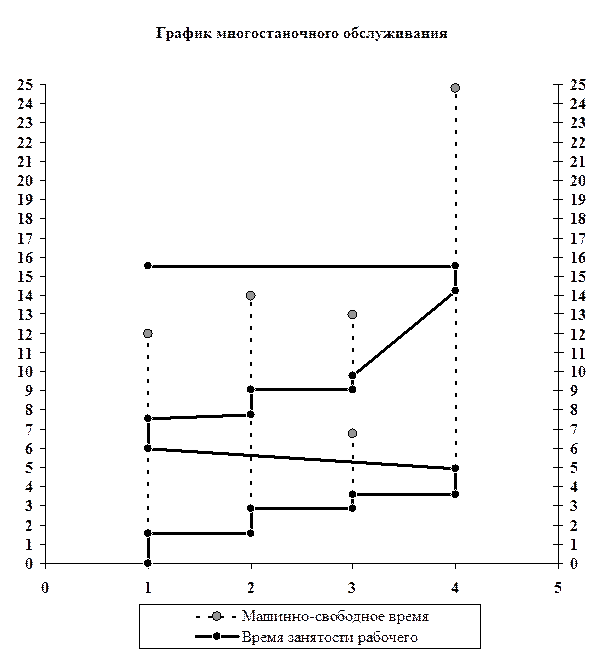
Определим суммарное время простоев оборудования в цикле многостаночного обслуживания (∑ Тпр) по формуле:
(2.12)
где: ∑ Топj – суммарное оперативное время выполнения детале-операций в цикле многостаночного обслуживания.
мин.
На основе полученных результатов расчетов установим коэффициенты загрузки оборудования, занятости рабочего, выполнения им установленных норм времени.
Занятость рабочего на рабочем месте многостаночника (Кзр) определим по формуле:
(2.13)
Загрузка оборудования рабочего места многостаночника (Кзо) определим по формуле:
(2.14)
Рассчитаем, сколько целых циклов многостаночного обслуживания уложится в сменном времени (результат расчета округлим в меньшую сторону):
(2.15)
Установим процент выполнения норм времени за смену (Пв.н..) рабочим-многостаночником:
(2.16)
3. Определение эффективности проекта
Целью расчета экономической эффективности является: обоснование лучших проектных решений; определение возможного прироста производительности труда и годового экономического эффекта от внедрения проектных решений; определение частных показателей эффективности внедрения проектных решений.
Рассчитаем снижение требуемой численности рабочих (Δ Чр) для выполнения производственной программы:
(3.1)
где: Чр.о и Чр.м – необходимая численность рабочих соответственно в условиях одностаночного и многостаночного обслуживания, шт.
(чел.) (3.2)
Определим снижение требуемого количества оборудования для выполнения производственной программы (Δ N):
(3.3)
где: Nн и Nн.м – необходимое количество станков в условиях одностаночного и многостаночного обслуживания, шт.
шт.
Рассчитаем повышение степени занятости рабочих в течение рабочего дня (Δ Кз):
(3.4)
где: Кз.м и Кз.о – коэффициенты занятости рабочих соответственно в условиях многостаночного и одностаночного обслуживания.
Рассчитаем снижение трудоемкости изготовления деталей (Δ Т) в часах:
(3.5)
где: Тшт и Тшт.м – норма штучного времени выполнения детале-операции соответственно в условиях одностаночного и многостаночного обслуживания, мин;
Р – месячная производственная программа изготовления деталей, шт.
Результаты расчета снижения трудоемкости приведены в таблице 9.
Таблица 9.
Расчет снижения трудоемкости изготовления деталей
№ детали |
Тшт, мин |
Тшт.м, мин |
Р, шт |
Δ Т, ч |
1 |
6,36 |
3,249079 |
500 |
25,9243417 |
2 |
3,71 |
1,825799 |
100 |
3,140335 |
3 |
3,24 |
2,914275 |
200 |
1,08575 |
4 |
7,776 |
2,226805 |
500 |
46,2432917 |
8 |
9,646 |
4,113422 |
200 |
18,4419267 |
9 |
5,512 |
2,72796 |
300 |
13,9202 |
10 |
6,572 |
2,835362 |
300 |
18,68319 |
11 |
1,802 |
2,60538 |
500 |
-6,69483333 |
12 |
8,532 |
1,798528 |
100 |
11,2224533 |
13 |
2,916 |
1,255686 |
100 |
2,76719 |
14 |
6,804 |
1,46034 |
100 |
8,9061 |
15 |
9,288 |
2,082903 |
100 |
12,008495 |
16 |
1,537 |
1,98792 |
100 |
-0,75153333 |
17 |
3,816 |
1,26948 |
500 |
21,221 |
18 |
6,048 |
1,999583 |
1000 |
67,4736167 |
19 |
5,184 |
2,52229 |
150 |
6,654275 |
20 |
4,212 |
1,114471 |
200 |
10,3250967 |
21 |
7,56 |
5,496096 |
600 |
20,63904 |
22 |
10,2384 |
2,129019 |
700 |
94,609445 |
23 |
9,504 |
2,259681 |
600 |
72,44319 |
24 |
4,104 |
5,175241 |
150 |
-2,6781025 |
25 |
2,184 |
3,132481 |
250 |
-3,95200417 |
26 |
3,068 |
4,0014 |
180 |
-2,8002 |
27 |
5,94 |
5,365256 |
1100 |
10,5369733 |
28 |
7,176 |
2,297584 |
1000 |
81,3069333 |
29 |
8,632 |
2,556842 |
900 |
91,12737 |
30 |
11,448 |
2,075224 |
400 |
62,4851733 |
Итого: |
684,3 |
Заключение
Таким образом, в ходе выполнения курсовой работы нами были выполнены следующие задачи:
1. Проведен анализ организационно-технических параметров объекта.
2. Установлены параметры исследуемого трудового процесса и время его выполнения.
3. Выявлены недостатки существующего трудового процесса.
4. Спроектирован рациональный трудовой процесс с установлением необходимого времени его выполнения.
5. Рассчитана экономическая эффективность внедрения рационального трудового процесса.
С экономической точки зрения разработанный нами проект является эффективным, так как его внедрение позволит снизить:
1. Необходимое число рабочих – до двух человек.
2. Требуемое количество оборудования для выполнения производственной программы – до пяти станков.
3. Трудоемкость изготовления деталей – на 1096,39 часов.
Список литературы
1. Базовая система микроэлементных нормативов времени. Методические и нормативные материалы. – М.: Экономика, 1989.
2. Беляев В.И. Концептуальная модель нормирования труда в функциональной структуре промышленного менеджмента. – Барнаул: АГУ, 1995.
3. Бычин В.Б., Малинин С.В., Шубенкова Е. В. Теоретико-методологические основы организации и нормирования труда // Нормирование и оплата труда в промышленности. №2, 2005.
4. Бычин В.Б., Малинин С.В. Нормирование труда: Учебник. / Под ред. Ю.Г. Одегова. – М.: Издательство «Экзамен», 2002.
5. Генкин Б.М. Организация, нормирование и оплата труда на промышленных предприятиях: Учебник для вузов. – М.: Издательство НОРМА, 2003.
6. Малинин С.В. Применение нормирования труда в повышении эффективности управления персоналом (статья) //Известия Академии труда и занятости. № 3-4, Ижевск, 2001.
7. Методика определения экономической эффективности мероприятий по НОТ. 3-е изд., доп. и перераб. – М.: Экономика, 1990.
8. Мосейчук М.А. Нормирование труда // Заработная плата, 2004. – № 2.
9. Общемашиностроительные нормативы времени для нормирования многостаночных работ на металлорежущих станках. - М.: Экономика, 1989.
10. Основы научной организации труда на предприятии / Под общ. ред. И.А. Полякова. – М.: 1997.
11. Применение базовой системы микроэлементных нормативов времени (БСМ) в организации и нормировании труда рабочих. (Методические рекомендации). – М.: НИИ труда, 1985.
- Суетина Л.М. Методы изучения затрат рабочего времени. - М.: НИИ труда, 1996.
[1] Генкин Б.М. Организация, нормирование и оплата труда на промышленных предприятиях: Учебник для вузов. – М.: Издательство НОРМА, 2003.
[2] Бычин В.Б., Малинин С.В., Шубенкова Е. В. Теоретико-методологические основы организации и нормирования труда // Нормирование и оплата труда в промышленности. №2, 2005. – с. 23
[3] Бычин В.Б., Малинин С.В. Нормирование труда: Учебник. / Под ред. Ю.Г. Одегова. – М.: Издательство «Экзамен», 2002. – с. 73
[4] Генкин Б.М. Организация, нормирование и оплата труда на промышленных предприятиях: Учебник для вузов. – М.: Издательство НОРМА, 2003.
[5] Бычин В.Б., Малинин С.В. Нормирование труда: Учебник. / Под ред. Ю.Г. Одегова. – М.: Издательство «Экзамен», 2002. – с.75
[6] Методика определения экономической эффективности мероприятий по НОТ. 3-е изд., доп. и перераб. – М.: Экономика, 1990. – с. 66
[7] Генкин Б.М. Организация, нормирование и оплата труда на промышленных предприятиях: Учебник для вузов. – М.: Издательство НОРМА, 2003. – с. 197
[8] Методика определения экономической эффективности мероприятий по НОТ. 3-е изд., доп. и перераб. – М.: Экономика, 1990. – с. 68
[9] Генкин Б.М. Организация, нормирование и оплата труда на промышленных предприятиях: Учебник для вузов. – М.: Издательство НОРМА, 2003. – с. 168