Внутрифирменный
менеджмент
(Краткий курс лекций).
Понятие менеджмента
В условиях рыночной экономики управление предприятиями значительно усложняется. Это связано как с расширением их прав и ответственности, так и с необходимостью более гибкой адаптации к изменениям в окружающей хозяйственной среде. Возникают новые цели и задачи, которые раньше организации самостоятельно не только не решали, но даже и не ставили.
Возникающие в связи с этим проблемы невозможно решить без современного профессионального менеджмента.
Менеджмент переводится на русский язык как управление производством и как совокупность принципов, методов, средств и форм управления производством с целью повышения его эффективности и прибыльности.
![]() |
Менеджмент определяется также как интеграционный процесс, с помощью которого профессионально подготовленные специалисты формируют организации и управляют ими путем постановки целей и разработки способов их достижения.
Процесс менеджмента предполагает выполнение функций планирования, организовывания, координации, мотивации, с помощью которых менеджеры создают условия для производительного и эффективного труда занятых в организации работников и получение результатов, соответствующих целям. Поэтому менеджмент – еще и умение добиваться поставленных целей, направляя труд, интеллект, мотивы поведения людей, работающих в организации. Это является основанием для рассмотрения менеджмента как процесса влияния на деятельность отдельного работника, группы и организации в целом с целью достижения максимальных результатов.
Умение ставить и реализовывать цели основатель школы научного менеджмента Ф. У. Тейлор определял как искусство точно знать, что предстоит сделать и как сделать это самым лучшим и дешевым способом. Этим искусством должна обладать определенная категория людей – менеджеры, чья работа состоит в организации и руководстве усилиями всего персонала для достижения целей.
Менеджмент – специфический орган современных организаций, как коммерческих, так и некоммерческих. Без него организация как целостное образование не может существовать и эффективно работать. Поэтому аппарат управления является составной частью любой организации и ассоциируется с понятием ее менеджмента. Главная же задача людей, занятых в этом аппарате – эффективное и скоординированное использование всех ресурсов организации (капитала, зданий, оборудования, материалов, труда, информации) для достижения ее целей.
В определении менеджмента как науки подчеркивается важность упорядоченных знаний об управлении. Они позволяют не только своевременно и качественно управлять текущими делами, но и прогнозировать развитие событий и в соответствии с этим разрабатывать стратегию и политику организаций. Они служат опорой при постановке задач и при осуществлении управленческой практики. Поэтому наука управления разрабатывает свою теорию, содержанием которой являются законы и закономерности, принципы, функции, формы и методы целенаправленной деятельности людей в процессе управления.
Понимание менеджмента как искусства управления базируется на том, что организации – это сложные социально-технические системы, на функционирование которых воздействуют многочисленные и разнообразные факторы как внешней, так и внутренней среды. Люди, работающие в организациях и с организациями – это самый главный фактор, учет которого требует не только использования научного подхода, но и искусства его применения в конкретных ситуациях.
Таким образом, в большинстве случаев используется понятие «менеджмент» как совокупность принципов, методов и средств управления предприятием с целью повышения эффективности его производства и увеличения прибыли.
Производственный менеджмент в системе менеджмента предприятия
Менеджмент предприятия предусматривает управление его разносторонней деятельностью, которая имеет объединяющую часть – производство. Другие направления деятельности предприятия предназначены обеспечивать нормальную работу по производству продукции или оказанию услуг.
Менеджмент предприятия
Þ Производственный менеджмент: (Планирование, организация и управление производством).
Производственный менеджмент предприятия можно представить как финансово-экономическое управление.
![]() |
Оно основано на трех китах: управление ассортиментом, себестоимостью и финансами. Все эти функции управления предприятием тесно связаны между собой благодаря постоянному обмену информацией, что позволяет видеть реальное положение дел в целом по предприятию.
Перечисленные функции управления не могут обходиться без структурированной информации. А добыча и обработка информации – это обязанность службы маркетинга на предприятии. Причем она не ограничивается только традиционным, так называемым внешним маркетингом, цель которого – сбор информации о ценах, конкурентах и многое другое. Не меньшее значение имеет и внутренний маркетинг, который занимается изучением собственного предприятия.
Функции производственного менеджмента
Сущность производственного менеджмента выражается в его функциях, то есть тех задачах, для решения которых он предназначен.
1. Планирование. Функцией менеджмента «номер один» общепризнанно считается планирование. Реализуя ее, предприниматель или управляющий на основе глубокого и всестороннего анализа положения, в котором в данный момент находится фирма, формулирует стоящие перед ней цели и задачи, разрабатывает стратегию действий, составляет необходимые планы и программы.
2. Организация. Реализация разработанных планов и программ входит в содержание других функций, и прежде всего функции организации. К ее «обязанностям» относятся создание фирмы, формирование ее структуры и системы управления, обеспечение ее деятельности необходимой документацией, организация собственно производственного процесса.
3. Координация. Фирма живет и работает благодаря занятым на ней людям, а их совместной деятельностью необходимо управлять. Поэтому важное значение приобретает функция координации трудовой деятельности людей.
4. Мотивация. Чтобы дела на фирме шли успешно, необходимы высокая активность и хорошее качество работы ее сотрудников. Поэтому очень важно заинтересовать их в таком отношении к труду, создать соответствующие мотивы.
5. Контроль. Суть пятой классической функции менеджмента – контроль. Он призван заблаговременно определять надвигающиеся опасности, обнаруживать ошибки, отклонения от существующих стандартов и тем самым создавать основу для процесса корректировки деятельности фирмы.
Методы производственного менеджмента
1. Организационные методы. Необходимо сначала создать фирму, расставить по местам людей, дать им задания, показать, как действовать, и уже после этого руководить их действиями.
2. Административные методы. На практике административные методы реализуются в виде конкретных безвариантных заданий, допускающих минимальную самостоятельность исполнителя, вследствие чего вся ответственность возлагается на руководителя, отдающего распоряжения.
3. Экономические методы. Позволяют исполнителям самим проявлять инициативу на основе материальной заинтересованности и отвечать за принятые ими решения. Исполнителю устанавливаются только цели и общая линия поведения, в рамках которых он самостоятельно ищет наиболее предпочтительные для него пути их достижения.
4. Социально-психологические методы. Сводятся к двум основным направлениям:
- во-первых, к формированию благоприятного морально-психологического климата в коллективе, способствующего большой отдаче при выполнении работы за счет повышения настроения людей;
- во-вторых, к выявлению и развитию индивидуальных способностей каждого, позволяющих обеспечить максимальную самореализацию личности в производственном процессе.
Производственные системы: понятие и закономерности
Производственная система представляет собой обособившуюся в результате общественного разделения труда часть производственного процесса, способную самостоятельно или во взаимодействии с другими аналогичными системами удовлетворять те или иные нужды, потребности и запросы потенциальных потребителей с помощью производимых этой системой товаров и услуг.
Возникновение той или иной производственной системы (ПС) обусловлено возникновением или формированием на рынке спроса на продукцию, способную удовлетворить требования покупателей.
В состав ПС любого уровня иерархии (предприятие, цех, участок, рабочее место) традиционно включают следующие ресурсы:
1. Технические ресурсы (особенности производственного оборудования, инвентаря, основных и вспомогательных материалов и т.п.).
2. Технологические ресурсы (гибкость технологических процессов, наличие конкурентоспособных идей, научные заделы и др.).
3. Кадровые ресурсы (квалифицированный, демографический состав работников, их способность адаптироваться к изменению целей ПС).
4. Пространственные ресурсы (характер производственных помещений, территории предприятия, коммуникаций, возможность расширения и пр.).
5. Ресурсы организационной структуры системы управления (характер и гибкость управляющей системы, скорость прохождения управляющих воздействий и т.п.).
6. Информационные ресурсы (характер информации о самой ПС и внешней среде, возможность ее расширения и повышения достоверности и т.п.).
7. Финансовые ресурсы (состояние активов, ликвидность, наличие кредитных линий и пр.).
В результате взаимодействия всех составляющих систему ресурсов получаются новые свойства, которыми каждый отдельный вид ресурса не обладает. Эти свойства обозначаются таким понятием, как эффект целостности системы.
В рыночной экономике существенную роль играет такой человеческий ресурс, как предпринимательская способность (предприимчивость). Это особый вид ресурса, который приводит в движение, организует взаимодействие всех остальных видов ресурсов ПС.
Предприятие как объект производственного менеджмента
Предприятие представляет собой производственную систему. С управленческой точки зрения его можно рассматривать как организацию, под которой понимается группа лиц, взаимодействующих друг с другом ради достижения общей цели с помощью различных вещественных, правовых, экономических и иных условий.
Люди и условия их деятельности в своей совокупности образуют то, что называется организационной структурой.
Организация как структура характеризуется рядом основополагающих признаков:
1) первым и едва ли не главным из которых является наличие цели, стоящей перед ней;
2) вторым признаком организации можно считать наличие в ней некоторого числа участников, которые, дополняя друг друга, объединяя свои усилия, помогая друг другу, обеспечивают реализацию ее цели;
3) такое единство действий членов организации достигается наличием внутреннего координирующего центра;
4) четвертым признаком организации является координация всех ее внутренних процессов на основе принципа саморегулирования (организационный центр самостоятельно принимает решения, касающиеся внутренней жизни организации, и координирует действия ее членов);
5) пятым признаком организации можно считать ее обособленность, наличие границ, отделяющих ее от внешнего окружения, в том числе от других организаций;
6) организационная культура, представляющая собой совокупность норм поведения, традиций, символов, словом, всего того, что отличает данную организацию от других.
Классификация объектов производственного менеджмента на предприятии
Производственная и экономическая деятельность определяет суть процесса функционирования каждого производственного предприятия.
Производство выступает как центральное ядро (сердцевина) производственного подразделения, созданное на основе рационального сочетания во времени и пространстве средств, предметов и самого труда, обеспечивающее при экономически обоснованном ведении производственного процесса его эффективное функционирование. Как объект управления производство является динамично развивающейся системой, указанные элементы которой взаимосвязаны и взаимозависимы. Они требуют четкого и целенаправленного взаимодействия.
Производственная структура предприятия.
Структура предприятия- это состав и соотношение его внутренних звеньев: цехов, отделов, лабораторий и других компонентов, составляющих единый хозяйственный объект. Структура предприятия определяется следующими основными факторами:
размером предприятия;
отраслью производства;
уровнем технологии и специализации предприятия.
Структура постоянно корректируется под воздействием производственно-экономической конъюнктуры, научно-технического прогресса и социально-экономических процессов.
Наряду с этим при всём многообразии структур все производственные предприятия имеют идентичные функции, главные из которых изготовление и сбыт продукции. Чтобы обеспечить нормальное функционирование, предприятие должно иметь в своём составе цехи или мастерские по изготовлению основной продукции (выполнению работ, оказанию услуг ) и по обслуживанию производственного процесса. Помимо того, каждое предприятие независимо от его размеров, отраслевой принадлежности и уровня специализации постоянно ведёт работу по оформлению заказов на изготовление продукции; организует её сохранность и сбыт заказчику; обеспечивает закупку и поставку необходимого сырья, материалов, комплектующих изделий инструмента, оборудования, энергоресурсов.
Наконец, чтобы каждый работник в любой отрезок времени делал именно то, что необходимо остальным и всему предприятию в целом, нужны управляющие органы, на которые возлагаются определение долгосрочной стратегии, координация и контроль текущей деятельности персонала, а также наём, оформление и расстановка кадров. Все структурные звенья предприятия, таким образом, связаны между собой с помощью системы управления, которая становится его главным органом.
На крупном предприятии указанные функции, как правило, разделяются на более конкретные обязанности отдельных подразделений. Скажем, основные цехи делятся на группы:
заготовительные;
обрабатывающие;
сборочно-сварочные (отделочные).
Отделы и лаборатории тоже непосредственно классифицируются в зависимости от конкретных задач. Так, группа технических отделов может включать до десятка отделов главного конструктора по каждому изделию, которое серийно выпускается на предприятии. Отдельно могут создаваться отделы главного технолога, главного металлурга главного сварщика и т.д.
Отраслевые особенности структуры предприятия
Структура предприятия непосредственно складывается под воздействием отраслевой технологии производства. Чем выше сложность технологического процесса, тем разнообразней и более громоздкой оказывается структура предприятия, а следовательно, и его размеры.
В повседневной практике сложность технологического процесса определяется:
-многообразием способов воздействия на предметы труда, необходимых для получения готового изделия;
-количеством технологических операций, которым подвергается изделие в процессе производства;
-уровнем предельной точности исполнения технологических операций.
Для машиностроительных предприятий в целом характерна сложная, многоступенчатая технология, а поэтому и наиболее громоздкая структура.
К одной из важнейших отраслевых особенностей структуры предприятия относится территориальное размещение производственных единиц. В отраслях обрабатывающей промышленности производственные и вспомогательные цехи, как правило, размещаются компактно на одной площадке, поскольку связаны технологическим процессом, жёсткими транспортными устройствами и не зависят от природного –климатических условий.
Профиль, масштабы, а также отраслевая принадлежность предприятия определяются составом, технологической специализацией и размерами его производственных цехов, участков, мастерских. Все другие звенья предприятия: функциональные отделы, лаборатории, управляющие органы, -полностью соизмеряются с характеристиками производственных подразделений и создаются исключительно для обеспечения эффективности их работы.
Производственные цехи (филиалы, участки, мастерские) разделены на 2 группы: цехи основного производства и вспомогательные и обслуживающие цехи. В цехах основного производства непосредственно изготавливается продукция, предназначенная для реализации.
Задача вспомогательных цехов –обеспечение нормальной, бесперебойной работы цехов основного производства. К вспомогательным относятся цехи и производственные участки по:
-изготовлению, ремонту, заточке и настройке инструментов, приспособлений, приборов, хозяйственного инвентаря;
-надзору за работоспособностью и ремонту оборудования, машин, механизмов, зданий и сооружений;
-обеспечению электрической и тепловой энергией, надзором и ремонтом электрооборудования и тепловых сетей;
-внутрипроизводственной и внешней транспортировке сырья, материалов, заготовок, готовой продукции,
-а также склады предприятия.
Конечный результат деятельности основных цехов – готовая товарная продукция, которая реализуется внешнему потребителю; конечный результат вспомогательных цехов потребляется внутри самого предприятия.
Цехи основного производства формируются в соответствии с профилем предприятия, а также в зависимости от конкретных видов продукции, масштабов и технологии производства. При этом неизменно ставятся задачи своевременного выпуска продукции, снижения издержек производства, повышения качества продукции, возможности своевременной перестройки производства в соответствии с быстро меняющимися потребностями рынка. Указанные задачи решаются на основе рациональной специализации и размещения цехов, их кооперирования внутри предприятия, обеспечения пропорциональности и единства ритма производственного процесса от первой до последней операции.
Существуют следующие формы специализации цехов: предметная; подетальная (поагрегатная); технологическая (стадийная).
Предметная специализация –это сосредоточение в отдельных цехах основной части или всего производственного процесса по изготовлению конкретных видов и типоразмеров готовой продукции. Общими для этих цехов являются единое инженерно-техническое обслуживание, материально-техническое обеспечение и сбыт продукции, складские помещения, что снижает их общие производственные расходы.
Подетальная (поагрегатная) специализация цехов, которая наиболее распространена в машиностроении, -это закрепление за каждым цехом изготовления отдельных деталей или агрегатов машин. Например, в специализированных цехах автомобильного завода отдельно изготавливаются двигатели, отдельно –коробка перемены скоростей, кабины и т.д. Все эти агрегаты передаются в цехи сборки, где из них собирается готовый автомобиль.
Технологическая (стадийная) специализация –это пооперационное разделение труда между цехами. При этом в процессе изготовления готовой продукции в каждом цехе используются различные технологии производства. Стадийная специализация цехов и участков широко используется почти во всех отраслях промышленности.
Понятие производственного процесса.
Принципы организации производственных процессов.
Производственный процесс представляет собой комплекс взаимосвязанных процессов труда, естественных процессов, направленных на изготовление продукции. Естественные процессы протекают без участия человека под воздействием внешних сил природы.
В каждом производственном процессе выделяют две стороны: технологическую и трудовую.
Технологическая сторона связана с превращением предметов труда в готовую продукцию или полуфабрикат с изменением физических свойств, геометрических форм и размеров, химического состава. Технологическая сторона находит выражение в заранее заданном технологическом процессе.
Трудовая сторона – это совокупность действий людей по осуществлению технологических процессов.
Организация производственного процесса предприятия предусматривает рациональное сочетание в пространстве и во времени основных, вспомогательных и обслуживающих процессов. Главная цель организации производственного процесса – экономия времени, обеспечение высокого качества и эффективности производства продукции.
Операция – часть технологического процесса, выполняемого на одном и том же рабочем месте, под одним и тем же предметом труда, одним и тем же инструментом и одним и тем же составом работающих. В производственном процессе выделяют основные и вспомогательные операции.
Основные операции направлены на изменение химического состава, свойств, геометрических размеров предмета труда (резание, термообработка, штамповка, механическая обработка, сборка и сварка).
Вспомогательные операции обеспечивают выполнение основных операций (транспортировка, установка, загрузка, контроль качества).
В сумме основные и вспомогательные операции образуют технологический процесс получения продукции.
Определение длительности производственного цикла.
Производственных цикл – отрезок времени между началом и окончанием производственного процесса, изготовление одного изделия или партии изделий.
Знать длительность производственного цикла необходимо для создания производственной программы, для определения сроков запуска в производство конкретных видов продукции по заданным или оговоренным в контракте сроком выпуска этой же продукции. Длительность производственного цикла используют при расчете величины незавершенного производства. Сокращение длительности производственного цикла имеет важное экономическое значение. Чем она меньше, тем при прочих равных условиях можно получить больший объем продукции, выше эффективность использования основных фондов, меньше потребность в оборотных средствах, которые вложены в незавершенное производство.
Рассматривая структуру производственного цикла выделяют 3 составляющих:
1. время выполнения операции (основных и вспомогательных)
2. время протекания естественных процессов
3. время перерывов.
Время выполнения основных операций, которые направлены на изменении геометрических размеров, формы, состава предметов труда образуют технологический цикл, который является основой производственного цикла (получение заготовки, её обработка, сборка и сварка).
Вспомогательные операции связаны с контролем технологических процессов, и с транспортировкой предметов труда в процессе обработки. Естественные процессы не требуют участия человека, но требуют затраты времени (вылеживание, сушка). В структуре простого процесса перерывы межоперационные (внутрициклические) делятся на: перерывы партионности и перерывы ожидания.
Перерывы партионности появляются тогда, когда передача с операции на операцию ведется партиями, и каждое изделие входящее в партию пролеживает ожидая окончания сборки всей партии.
Перерыв ожидания появляется в результате диспропорции по производительности на смежных операциях.
Факторы, влияющие на длительность производственного процесса:
1. Конструкторско-технологические. Чем сложнее конструкция, тем больше число простых процессов, тем сложнее организовать взаимосвязь процессов, полную загрузку оборудования и минимальное пролеживание в процессе обработки.
2. Организационного характера. Организация процессов во времени, организация рабочих мест, уровень механизации – автоматизации производственных процессов.
3. Экономического характера. Уровень организации трудовых процессов, рациональных форм стимулирования труда, мотивации трудовой деятельности, уровень оснащенности рабочих мест и др.
Основу производственного цикла составляет цикл технологический, который состоит из циклов операционных.
Операционный цикл – это продолжительность обработки одного изделия (партии) на одной операции процесса. Его определяют исходя из затрат времени:
1. на изменение структуры, свойств и состава предмета труда (основное время).
2. затраты времени на выполнение вспомогательных приемов (загрузка, выгрузка, включение и т.д.)
Эти затраты времени повторяются при изготовлении каждого изделия, поэтому их относят к ед. продукции и называют штучным временем (tшт ).
Т.О. операционный цикл при
изготовлении одного изделия равен: .
При обработки партии:
Если на одной операции задействовано несколько рабочих мест то
, где
Сi – количество рабочих мест одновременно занятых на одной операции.
Величина технологического цикла во многом зависит от выбранного сочетания во времени операционных циклов.
Рассматривается 3 способа передачи предмета труда:
1. последовательный (наиболее простой)
2. параллельно-последовательный
3. параллельный
1. Последовательный
Основное условие: каждая последующая операция над изделием (партией) начинается после окончания обработки изделия (партии) на предыдущей операции. Наблюдаются перерывы партионности, поэтому рационально использовать этот вид передачи при небольших партиях и невысокой трудоемкости. Используются в единичном и мелкосерийном производстве.
N операций
1
2
3
t, мин
Тт.ц. –длительность технологического цикла
n – количество изделий
tшт i – время i-ой операции
m – количество операций процесса
i –количество рабочих мест на i –ой операции технологического процесса
2. Параллельно -последовательный
Предусматривает такой порядок работ при которой достигается наибольшая одновременность выполнения смежных операций и при этом обеспечивается непрерывность обработки всей партии изделий на каждой операции.
Партия изделий в n штук делиться на более мелкие передаточные партии (P), именно это позволяет выполнять условия непрерывной и одновременной обработки.
При организации процесса во времени рассматривается варианты сочетания смежных операционных циклов.
Р
– малая транспортная партия
Рi
Pi+1
Рi и Pi+1 –время обработки одной транспортной партии на i и i+1 операции
Τпер – время перекрытия
а) Nоп
|
|||
|
|||
i
τпер
i +1 Р1 Р2 Р3 Р4
t, мин
б)
Nоп
P1 P2 P3 P4
i
τпер
![]() |
i+1
t, мин
При построении графика процесса производится по парное сравнение смежных операций и в каждой паре выбирается операция с минимальным операционным циклом
Длительность технологического цикла при II/постоянной обработки значит меньше чем при последовательном виде передачи, но при этом появляется большее число планово учетных единиц и увеличивается нагрузка на транспортное средство.
Целесообразно использовать при небольших партиях и значительной трудоемкости обработки. Это свойственно крупносерийному типу производства.
3. Параллельный
Параллельный тип характеризуется тем, что небольшие передаточные партии передаются с предыдущей операции на последующую немедленно после окончания обработки на предыдущей операции. При этом партии изделий в процессе обработки не пролеживают, а рабочие места загружены не всегда полностью вследствие разницы по производительности. При построении графической модели сначала устанавливают операцию имеющую наибольшую производительность. Процесс обработки на этой операции будет непрерывным в отличии от других операций.
Nоп.
Р1 Р2 Р3 Р4
1 Х Х Х
Р1 Р2 Р3 Р4
2
Р1 Р2 Р3 Р4
3 Х Х
Х
Р1 Р2 Р3 Р4
4 Т max. у. Х Х Х
![]() |
t,мин
Не целесообразно применять для процесса с различной длительностью операций т.к. потери времени могут быть значительными.
Для устранения потерь надо проводить выравнивание операционных циклов, и если достигается синхронизация - это переход к непрерывно-точной форме организации производства.
Определяя длительность производственного цикла в основу закладывают длительность технологического цикла, а время выполнения операций вспомогательных учитывают только в том случае, если их выполнение не перекрывается циклом технологическим или временем перерывов в обработке.
Для удобства разработки планов-графиков длительность технологического процесса рассчитывают в днях. Для этого надо определить коэффициент перевода в календарные дни:
где 1,4 –коэффициент для
прерывистых графиков работы подразделений
Длительность производственного цикла(Тп.ц.):
, (дн)
Большинство процессов имеют сложных характер и состоят из процессов простых – получение элементов входящих в общее изделие. При реализации сложных процессов простые могут сочетаться во времени последовательно, последовательно-параллельно и параллельно. Построение моделей сложных процессов во времени производится для достижения следующих целей:
1. определить длительность производственного цикла сложного процесса который используется при разработки оперативных плановых графиков производства.
2. чтобы установить какие детали (узлы) могут изготавливать параллельно.
3. определить время начала запуска производства деталей, узлов.
Взаимосвязь простых процессов получения конструкции изображается с помощью веерных диаграмм с выделением уровня иерархии.
![]() |
К конструкция
![]() |
УI УII узел
Д1 Д2 Д3 Д4 Д5
При построении необходимо выяснить какие производственные мощности используются, загружены они или нет в данный момент времени и возможна ли параллельная обработка (сборка) всех элементов конструкции. Время запуска производства определяется из времени выпуска. Если изготовление деталей, сборка узлов и конструкции не лимитируется составом оборудования, то возможна максимальная параллельность.
![]() |
|||||||||
|
|||||||||
![]() |
![]() |
||||||||
|
|||||||||
|
|
|
|
|
|



























При определении длительности производственного цикла сложного процесса учитываются межциклические перерывы. Рассчитывается коэффициент параллельности процесса.
Пути сокращения длительности производственных циклов.
Длительность производственного цикла в практике сокращают по двум направлениям: сокращают рабочий период и полностью ликвидируют или сводят к минимуму различные перерывы.
Мероприятия по сокращению длительности производственного цикла вытекают из принципов построения производственного процесса.
Сокращение рабочего периода в части операционных циклов достигается путём совершенствования технологических процессов, повышения технологичности конструкции.
Совершенствование технологических процессов –их комплексная механизация и автоматизация, внедрение скоростных режимов применение прогрессивных технологических процессов, концентрация операций.
Концентрация операций заключается в многоинструментальной и многопредметной обработке или в совмещении в одном рабочем цикле нескольких технологических операций.
Повышение технологичности –рациональное разделение конструкции на узлы для параллельной сборки.
Продолжительность транспортных операций может быть значительно уменьшена в результате перепланировки оборудования на основе принципа прямоточности.
Время межоперационных перерывов значительно уменьшается в результате перехода от последовательного к последовательно-параллельному и параллельному виду движения
Полное отсутствие перерывов партионности и обслуживания характеризует непрерывно-поточное производство. Межоперационные перерывы могут быть уменьшены путём организации цехов предметной специализации.
Поточная форма организации производства.
1. Поточное производство, основные виды, характеристика, организационные формы.
2. Основные элементы расчета и организации поточных линий.
2.1. Особенности организации непрерывно поточных линий.
2.2. Особенности организации прямоточных линий.
2.3.Особенности многопредметных поточных линий.
2.4.Особенности организации автоматических поточных линий.
Экономическая эффективность использования поточных форм организаций производственных процессов состоит в повышении производительности труда в следствии факторов, реализация которых возможна наиболее полно в условиях потока – использование специализированного оборудования и оснастки, механизация транспортных работ, специализация рабочих мест, оптимальный уровень обслуживания рабочих мест . Это приводит к сокращению потерь рабочего времени и оптимизирует процесс обработки, даёт уменьшение объема незавершенного производства, улучшение использования основных фондов предприятия и его подразделений, загрузку оборудования, повышение качества продукции, снижается брак. Все это приводит к снижению затрат на выпуск продукции, увеличению прибыли предприятия и повышению рентабельности производства. Применение поточной формы организации производства основано на принципах:
1) Специализации, создание предметно-замкнутых участков в виде специализированных линий для выполнения технологических ,транспортных и контрольных операция. За линией м.б. закреплено одно изделие – однопредметная линия (характерна для массового типа производства), если производство носит серийный характер, то за линией закреплено несколько изделий и тогда она называется многопредметной или многономенклатурной.
2) Прямоточность состоит в расположении рабочих мест, основного технологического оборудования в порядке следования технологического процесса. Цепочка рабочих мест м.б. простой: одна операция одно рабочее место и сложной - на операции несколько рабочих мест-дублёров. При организации сложных цепочек появляется проблема адресования изделий по рабочим местам.
3) Непрерывности на поточных линиях реализуются в виде непрерывного движения изделий по операциям, при непрерывной работе рабочих и оборудования. Такие линии называются непрерывно-поточные, они м.б. одно- и многопредметными. Реализуются непрерывность потока вследствие принципа пропорциональности -равной производительности на всех операциях процесса. Равная производительность обеспечивает полную загрузку рабочих мест и рабочих. Если вследствие технических и технологических особенностей не удается достичь равной производительности, то линия работает как прерывнопоточная или прямоточная. М.б. одно и многопредметные
4) Параллельности -параллельность движения изделий или партии изделий т.е. в каждый момент времени на линии обрабатывается несколько изделий данного вида на разной стадии технологического процесса.
5) Ритмичности - т.е. ритмичный выпуск продукции с линии и ритмичное повторение операций. Операции наибольшей продолжительности должны иметь большее число рабочих мест-дублеров.
|
4 4
|


2
мин 2
|


Чем шире русло потока тем медленнее ведется обработка. Этим и достигается единый такт работы линии, т.е. выпуск одного и того же количества изделий через равные промежутки (интервалы) времени.
На прямоточных линиях с различной производительностью по операциям непрерывность работы оборудования отсутствует , но ритмичность выпуска продукции соблюдается .
По способу ритмичности разделяются линии :
- с регламентируемым ритмом (непрерывно поточное)
- свободным ритмом (прямопоточное)
Наиболее распространенным транспортным оборудованием в поточном производстве является транспортное оборудование непрерывного действия ( конвейеры).
Могут использоваться спуски, скаты, подъемно-транспортное оборудование циклического действия (кран-балки, мостовые краны).
Конвейеры могут быть:
1) рабочие - служат для выполнения технологических операций на конвейере. Широко используются в сборочном производстве;
2) распределительные - обслуживают линии со стационарными рабочими местами для адресования изделий по рабочим местам.
Основные элементы организации поточных линий:
1.r - такт работы линии – это интервал времени между запуском на линию данного объекта и объекта следующего за ним. Такт определяется с учетом регламентированных перерывов связанных с обслуживанием оборудования и с учетом брака который может быть обнаружен при конечном контроле
Тсм –продолжительность смены
Тр.п. –продолжительность регламентированных перерывов
f – количество смен работы в сутки
Nзапуск. = Nвып.(1+α), α - % брака (удельный вес)
Если на линии одновременно собирается или вырабатывается несколько единиц продукции однотипных и при этом передача с одной операции на другую осуществляется передаточными партиями Р, то рассчитываем ритм работы линии
R = р · r
2. Число робочих мест на каждой операции.
Если числа получились не целые, то устанавливают принятое число рабочих мест Спр округляя расчетную величину до ближайшего целого числа.
3.) Коэффициент загрузки оборудования на каждой операции
Средний коэффициент загрузки оборудования, который установлен на всей линии
Если Срасч.=Спр., то можно определить число операторов на линии.
Учитывая число рабочих смен, рабочих мест и норму обслуживания рабочего места.
Выбор типа линии
Если соблюдаются условия:
,
то линия работы по принципу непрерывного потока. Если условие не выполняется, то линия будет прямоточной. Допускается перегруз рабочего места на 8-10% на этапе проектирования. Далее снятие этого перегруза при синхронизации операции. Наиболее распространенными способами синхронизации м.б.:
1. Расчленение операций на переходы и комбинирование различных вариантов выполнения перехода или группировка переходов в несколько операций;
2. концентрация операций при оснащении линий комбинированным оборудованием;
3. введение параллельных рабочих мест на тех операциях, где прослеживается кратность времени выполнения такту работы линии.
4. интенсификация режимов обработки, совмещение времени машинной и ручной работы;
5. совершенствование рабочих приемов на ручных операциях.
Особенности расчета непрерывно-поточных линий (НПЛ).
Планировка непрерывно-поточной линии начинается с разработки схем рабочих мест, выбора транспортных средств и средств промежуточного контроля, а также мест для формирования заделов.
Основное транспортное средство и НПЛ – конвейер, м.б. распределительными и рабочими.
Шаг конвейера – длина одного деления – это расстояние между осями симметрии двух рядом расположенных объектов. Шаг конвейера выбирается из соотношения:
lmin устанавливается с учетом габаритов изделия и расстояния между двумя смежными изделиями.
Lш.max определяется допустимой скоростью движения конвейера. Для конвейеров с постоянным рабочим ритмом движения V = 0,5 – 2 м/мин.
Скорость движения конвейера должна соответствовать такту потока – это достигается, если путь равный одному шагу конвейера проходит за один такт
lш = Vк∙rНПЛ
Если цепочка простая согласования не требуется.
При сложных технологических цепочках разрабатывается система адресования.
Длина рабочей части распределительного конвейера:
где Сpi –рабочие места;
Сki –места технологического контроля
Общая длина ленты конвейера
где D –диаметр натяжного барабана.
Для рабочих конвейеров нормальную длину рабочей зоны (станции) операции определяют:
На операциях со значительными колебаниями времени выполнения предусматривается резервная зона.
На НПЛ образуется 3 вида заделов:
1.
технологический задел соответствует количеству изделий
которые в каждый момент времени находятся в процессе обработки на рабочих
местах. Задел равен числу рабочих мест.
2. транспортный задел. Его образуют изделия, находящиеся в каждый момент времени в процессе транспортировки. Равен числу рабочих мест минус 1.
3. страховой. Задел на более ответственных операциях, определяется экспериментальным путем, не превышает 4-5% сменного задания.
Особенности расчета прямоточных линий (ПЛ).
На ПЛ различная трудоемкость обработки по операциям технологического процесса, синхронизации не поддаются, но имеет смысл такую линию разрабатывать если обеспечивается синхронизация на большей части процесса и возможна комбинированная загрузка рабочих мест.
Определяется размер и динамика межоперационных оборотных заделов.
Укрупненный ритм –это время в течении которого формируется выработка продукции в количестве, соответствующему плановому заданию. При этом необходимо учитывать периодичность передачи продукции с одного участка на другой, а также частоту перехода рабочих с одного рабочего места на другое. Межоперационные оборотные заделы образуются в результате различной производительности оборудования на смежных операциях, определяется как разность числа изделий обрабатываемых на смежных операциях за период неизменных по производительности условий.
Тн.у. – период времени неизменных по производительности условий
Если «+»Z, то это означает что за
период неизменных условий он вырастает до
положительной расчетной величины, т.к. с предыдущей операции поступает больше
изделий чем м.б. обработано на последующей, т.е. производительность предыдущей
операции, выше чем последующей.
Если «-»Z – убывание задела и необходимость его создания к началу периода неизменных условий по производительности. Это вызвано тем, что с предыдущей операции на этом отрезке времени неизменных по производительности условий поступает изделий меньше, чем необходимо для непрерывной работы оборудования на смежных операциях техпроцесса.
20+ -15
-5
Тн.у.
График-регламент работы прямоточной линии.
№ операции |
tшт |
Ср |
Спр |
Кз/м% раб. мест |
№ рабочего |
|
1 |
4 |
1 1 |
2 |
100 100 |
№1 №2 |
|
2 |
1,7 |
0,85 |
1 |
85 |
№3 |
|
3 |
1,8 |
0,9 |
1 |
90 |
№4 |
|
4 |
0,3 |
0,15 |
1 |
15 |
№5 |
Период формирования задела
![]() |
Nоперац. R 120
30 60 90 102′
108′ 120
![]() |
1
Т ́1-2(2;1)
Т″1-2(2;0)
![]() |
2 Т′2-3(1;1) Т″2-3(0;1)
3
Т′3-4(1;0)
4 Т″3-4(1;1) Т″′3-4(0;1)
Fсм = 480¢
Тпер = 20¢
Nзон = 220шт
nобол. раб.м. = 1 чел (норма обслуживания)
Nоперац. 1 – 2
Z¢ = ((102 × 2)/4) – ((102 × 1)/1,7) = -9
Z²= ((18 × 2)/4) – ((18 × 0)/1,7) = +9
2 - 3
Т¢ Z¢ = +3
Z² = -3
Z²¢ = 0
3 – 4
Z¢ = +57
Z² = -17
Z²¢ = -40
N опер |
|
0 30 60 90 102 120 |
|
|
|
|
|
|
|
|
|
4 |
Особенности расчета многопредметных поточних линий.
Многопредметные линии характерны для серийного типа производства. За каждой линией закрепляется несколько технологий однородных изделий. Такие линии должны обладать быстротой и гибкостью переналадок оборудования. Такты работы линии могут сохраняться или изменяется при переходе от одного изделия к другому. Если за линией закрепляются изделия с одинаковой трудоемкостью, то обработка будет с единым тактом. Такты работы линии определяются исходя из суммарной программы запуска по всем изделиям, закрепленным за линией. Если за линией закреплены изделия с различной трудоемкостью, то целесообразно вести обработку этих изделий с различными тактами. Частные такты определяются:
1) если все рабочие места участвуют при обработке всех изделий, то частный такт можно определить исходя из неизменного числа рабочих мест на линии и трудоемкости обработки. Общее число рабочих мест на линии (с) определяется делением трудоемкости всей программы выпуска (Т) на фонд времени работы оборудования (Фобр.):
Ф – фонд времени работы оборудования.
Ni –годовой объем производства продукции i-го вида.
Тогда частый такт при условии, что С=const
;
;
2) Приведение программы к условному объекту.
Для этого выбирается наиболее типичное изделие, трудоемкость которого принимаем за 1 (tбаз.)
Коэффициенты трудоемкости определяем для каждого изделия:
Определяем условную программу выпуска по каждому виду продукции:
Условный такт
:
Такт для i-го изделия: ri = rуслов.· Kтрудности i
3) Распределение общего фонда времени работы оборудования по объектам обработки.
Трудоемкость годового выпуска i-го вида продукции.
Трудоемкость обработки всей программы в n-изделии.
Фонд времени обработки i –го вида продукции
Фдоб – фонд времени действия оборудования.
ТS - суммарная трудоемкость.
- частный такт работы
линии ri.
Niзап – программа запуска по i-му виду продукции.
Организация работы серийных не поточных предметно-замкнутых участков.
1. Минимальный размер партии:
где
-коэффициент
допустимых потерь времени на переналадку оборудования.
Это соотношение устанавливается на той операции, для которой оно будет наибольшим и принимается для всех остальных операций. Расчетное значение корректируется в соответствии с производственными условиями и после корректировки размер обрабатываемой партии изделий должен быть:
1) во-первых равным или кратным месячной программе запуска изделий;
2) во-вторых равном или кратным фактической производительности в смену и не должен быть меньше полусменной выработки рабочего на наименее трудоемкой операции. В результате проведенной корректировки получаем нормативный размер партии, ng.
2. Периодичность запуска
– выпуска исходя из месячной программы запуска и размера партии , где R – период повторения
обработки.
3. Длительность производственного цикла и технологического цикла устанавливают на партию изделий.
4. Величина задела определяется делением длительности производственного цикла на период повторения и выражается в целых партиях запуска изделий в производство
Если Тц < Rз, то Z не более одной партии.
Тц. кратна Rз, то Z = целому числу.
Для определения даты выпуска необходимо знать величину задела Z на начало месяца и дневной выпуск изделий. Дата запуска первой партии определяют вычитая из даты выпуска Т цикла производства.
Техническая подготовка производства.
1. Научно исследовательские работы.
2. Опытно-конструкторские разработки.
3. Технологическая подготовка производства (разработка технологической документации).
Плановые расчеты технической подготовки производства (ТПП).
При планировании работ технологической подготовки производства можно использовать ленточные графики Ганта и сетевые методы планирования и управления (СПУ).
Для координации во времени всех стадий этапов ТПП с учетом возможного совмещения или параллельного выполнения во времени составлению ленточных графиков. График составляется от заданного срока окончания разработки в обратной последовательности имеет ряд недостатков:
На ленточном графике не возможно показать взаимосвязь работ, поэтому может проявиться простои, несогласованность выполнения сопряженных работ.
На ленточном графике затруднён контроль состояния выполнения работ и сложно вносить изменения в сроки и выполнения.
Ленточный график не обеспечивает равномерную загрузку исполнителей. На графике не возможно отразить неопределенность, которая часто присуща научно-исследовательским и конструкторским работам.
Все перечисленные недостатки позволяет устранить система сетевого планирования и управления (СПУ).
СПУ основана на графическом изображении определенного комплекса работ в логической последовательности и взаимосвязи.
В настоящее время наиболее разработаны системы СПУ, в которых в качестве исходной информации используется временной параметр.
Модели всего процесса в системе СПУ изображаются в виде ориентированного в пространстве графа (тетраэдра) без контура. Ребра графа изображают работы. Поскольку граф ориентирован в пространстве они изображаются стрелкой.
Работами называют процессы или действия, которые приводят к достижению промежуточных результатов.
Промежуточный результат в систему СПУ называется событием.
Событие – это момент завершения нескольких работ или одной работы. На графике события находятся на вершинах графа и обозначается кружочками, чтобы можно было поставить его номер.
Намечая промежуточные результаты (события) формулируют в совершенной форме. (например: принято решение, закончена разработка и т.д.).
Номеруются события одним числом в последовательности выполнения от нулевого (исходного) события к событию завершающему.
Работы заключены между событиями и их нумерация или кодирование состоит из 2-х чисел; 1-е число всегда меньше второго, т.к. номер события у острия стрелки всегда больше чем у основания.
Последовательность нумерации событий.
![]() |
|
|
|

|
|







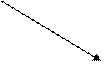




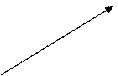

|
Если необходимо показать взаимосвязь событий, но при этом не требуется затраты времени для выполнения работы, то её показывают пунктирной линией (фиктивная работа).
Каждая линия которая соединяется исходящее событие и конечное называется полным путём 0-1-4-5
0-2-3-5
0-3-5
Особое внимание заслуживает путь критический, который требует наибольшего времени для своего выполнения. Критический путь определяет общий цикл завершения всего комплекса работ. На работах критического пути сосредоточенно внимание руководства в процессе управления разработкой.
Правила построения сетевых моделей.
Надо выполнить условия:
1. Составить перечень всех работ, которые необходимо выполнить.
2. Наметить промежуточные результаты или события, ответить на вопросы:
- какие работы могут (должны) быть закончены прежде, чем можно будет преступить к выполнению данной работы?
- какие работы можно вести параллельно с данной работой?
- возможность начала каких работ зависит от завершения данной работы?
Ответив на эти вопросы, обычно получают систему шифров работ, используя эту систему и строят сетевую модель.
Сетевые модели составляют для 30 – 50 работ.
Построив сетевую модель проверяют правильность построения
- убирают тупиковые события – от которых не начинается ни одна работа,
- убирают замкнутые контуры, в которых каждая работа предшествует сама себе,
- убирают хвостовые события, дублирующие исходное событие,
- убирают одинаковые коды работ, которые находятся между одними и теми же событиями.
Определение продолжительности выполнения работ.
В зависимости от характера выполнения работ время выполнения их могут устанавливать по нормативам, и тогда модель времени принимает детерминируемый характер и могут устанавливать экспертным путем. В этом случае модель вероятностная. Второе направление предусматривает определение группы экспертов которые устанавливают продолжительность выполнения каждой работы несколькими вероятностными оценками. Таких оценок может быть 2: min и max время выполнения работ.
Min время составляет благоприятные условия выполнение работ, а max – неблагоприятным.
Или определяется по 3 оценкам: max, min и наиболее вероятным.
По этим оценкам рассчитывают ожидаемое время выполнения работ(tожид). Величина tожид представляет
собой математическое ожидание случайной величины. Распределение случайной
величины охарактеризует дисперсия (мера неопределённости
данного распределения). При принятом в СПУ законе
-распределения,
дисперсия
определяется как 1/6 размаха в квадрате (если используется 3
оценки).
Размах – это разность tmax - tmin
Чем >σ2t, тем меньше вероятность того, что работа будет выполнена в заданный срок.
Если σ2t соответствует нормам, то можно расcчитать tожид.
Если используется 3 оценки, то
Если используется две оценки, то
Расчетная величина tожид. проставляется на графике над стрелкой, которая изображает работу (в днях, часах).
Расчет параметров сетевой модели.
1. Расчет параметров событий.
2. Расчет критического пути.
3. Расчет параметров работ и определение резервов выполнения работ.
Расчет параметров сетевой модели можно вести на графике, с помощью таблиц и с помощью ЭВМ.
Наиболее наглядный графический метод:
i j
Tpi Tni ti-j Tpj Tnj
Ri Rj
В верхнем секторе проставляется номер события; в левом секторе – ранний срок наступления данного события; в правом – поздний срок наступления события; в нижнем – резерв времени совершения данного события; над стрелкой – продолжительность работы.
Ранний срок наступления события – минимальный из возможных сроков наступления данного события при заданной продолжительности работ. Ранний срок исходного события всегда равен нулю. Ранние сроки последующих событий определяют прибавлением к ранним срокам предыдущих событий продолжительности работ, ведущих к данному событию.
Если через событие проходит насколько работ, то при расчете раннего срока выбирается наибольшее значение продолжительности пути ведущего к данному событию.
Поздний срок свершения события рассчитываются от завершающего события к исходному в обратном порядке. Для события завершающего, поздний срок равен раннему сроку этого же события.
Поздний срок – максимальный из допустимых сроков наступления данного события при котором еще возможно выполнение всех последующих работ.
Для определения позднего срока предыдущего события из позднего срока последующего события вычитают продолжительность i-j-работы.
;
Это время находят выбирая минимальное значение из продолжительности всех путей выходящих из данного события в обратном направлении – от завершающего к данному событию.
Резерв времени события – это промежуток времени на который можно перенести срок наступления данного события не нарушая сроков окончания всей разработки. Определяется резерв времени события как разность между поздним сроком данного события и ранним сроком данного события.
Если резерв времени равен нулю, то данное событие относится к пути критическому. Критический путь – протекающий от события исходного к завершающему через событие имеющее нулевой резерв времени свершения.
Эти события должны наступить в четко указанный или определенный срок. Если он будет изменен, то это приведет к изменению всей разработки.
Поэтому процессы управления сосредоточенны на работах критического пути.
Работы, которые не лежат на критическом пути также имеют резерв времени, который позволяет маневрировать сроками начала и окончания работ, а также изменять их продолжительность.
Для определения резервов времени работ вначале устанавливают параметры работ: ранний и поздний сроки начала и окончания работ. Параметры работ заносят в таблицу.
1) Ранний из возможных сроков начала данной работы равны раннему сроку того события из которого данная работа выходит
2) Ранний из возможных сроков окончания работы равен раннему сроку свершения предшествующего данной работе события плюс продолжительность i-j работы:
3) Позднее из допустимых сроков окончание i-j работы равно позднему сроку свершения события, к которому ведет данная работа:
4) Позднее из допустимых сроков начала i-j работы равно позднему сроку свершения события, к которому ведёт данная работа – продолжительность i-j работы:
Определяют 4 вида резервов времени работы:
1. полный
2. частный I-го и II-го рода
3. свободный.
Полный резерв – запас времени, которым можно располагать при выполнении данной работы если предшествующее событие свершилось в его самый ранний срок и можно допустить, что событие к которому ведет данная работа свершиться в его самый поздний срок.
Полный резерв – максимальный резерв времени для выполнения данной работы. В пределах этого резерва можно увеличивать продолжительность выполнения данной работы. Но если использовать этот резерв частично или полностью, то соответственно уменьшиться резервы времени всех работ лежащих на данном пути, т.к. этот резерв принадлежит всем работам пути.
Частный 1-го рода – показывает, какая часть полного резерва времени выполнения работы можно использовать для увеличения продолжительности данной работы не влияя на ранние сроки начального для данной работы события.
Частный 2-го рада – показывает, какую часть полного резерва времени выполнения работы можно использовать для увеличения её продолжительности, не влияя на поздний срок конечного для данной работы события.
Свободный резерв определяет на сколько можно увеличить продолжительность работы не изменяя при этом ни ранних сроков совершения исходного для данной работы события, ни поздние сроки конечного для данной работы события.
![]() |

i tij j
Tpi Tni Tpj Tnj
Ri Rj
Менеджмент трудовых процессов.
Управление производством осуществляется через посредства людей от уровня квалификации, от выбранных направлений, кооперации и разделения, от выбранных направлений и мотивации трудовых процессов зависит результативность труда.
Организация труда решает три основных задачи:
1. Экономическая, связанная с повышением уровня производительности труда и получения продукции того же объема при меньших затратах труда.
2. Психофизическая, т.е. сохранение в процессе труда здоровья и трудоспособности человека.
3. Социальная (удовлетворять работой).
Для решения этих задач необходимо: во-первых, разработка рациональных форм разделения и кооперации труда; во-вторых, оптимизация условий труда; в третьих рациональная организация обслуживания рабочих мест; в четвертых – подбор, подготовка и расстановка кадров; в пятых – разработка научно-обоснованных форм и нормативов трудовых процессов; в шестых – использование мотивов и стимулов трудовой деятельности каждого работника в целях повышения его заинтересованности в результатах работы предприятия в целом.
Разделение труда – это распределение работ между исполнителем, которое способствовало бы:
- специализации работников и приобретению ими определенных навыков, опытов, знаний, умений.
- ответственности каждого работника за порученною работу.
- четкое взаимопонимание между работниками, т.е. условия кооперации при выполнении общего комплекса работ
Конкретные формы разделения труда определяются структурой производственного процесса или управлением.
Направления разделения труда:
1. функциональное – направление, исходящее из разделения трудового процесса согласно их производственному назначению и характеру выполняемых функций. В соответствии с этим персонал предприятия делиться на категории работающих: специалисты (руководители), рабочие основные и вспомогательные
2. технологическое определяется разделением трудового процесса на технологически однородные операции, которые выполняются одним рабочим или группой рабочих. В соответствии с этим персонал делиться по профессиям.
3. квалификационное разделение предполагает специализацию исполнителей в зависимости от их умения и уровня подготовки. Предполагает введение разрядов д. рабочих и категорий для специалистов.
Это все связывается в кооперацию.
Кооперация имеет разнообразные формы: бригадные, совмещенные профессии, многоагрегатное обслуживание.
При разделении и кооперации необходимо установить результаты работы, установить уровень качества выпускаемой продукции и методы контроля за качеством. В процессе расстановки рабочих по рабочим местам за каждым исполнителем закрепляется рабочее место, круг функциональных обязанностей, учеты и оценка результатов работ.
Использование бригадных форм:
1. Целесообразно использовать бригадную форму труда. Когда один агрегат обслуживается несколькими работниками и результат их работы, то, что выдается (термическая печь, кузнечное, литейное оборудование).
2. Целесообразно использовать бригадную форму специализации труда, когда рабочие обслуживают сложные комплексные работы, которые сложно разделить на отдельные составляющие (сварочные работы крупногабаритных конструкций, выполнение ремонтных работ сложного технологического оборудования).
3. Выполнение взаимосвязанных работ в поточных формах производства.
4. Взаимное выполнение основных и вспомогательных работ. Входят рабочие наладчики, транспортные рабочие.
В зависимости от характера технологического процесса и профессионального состава рабочих выделяется бригады специализированные, комплексные.
Специализированные создаются из рабочих одной профессии, выполняющих однородную технологическую операцию и работающих по одному наряду. Тип таких бригад организуют при выполнении ручных и неполных механизированных работ на участках технической специализацией.
Комплексные состоят из рабочих различных профессий, ориентированных на выполнение определенной производственной цели. Создаются на участках с предметной специализацией. Комплексные бригады могут создаваться в случаях неодинаковых пропорций в затратах труда отдельных исполнителей. При этом широко используются совмещение профессий, которое обеспечивает более полную загрузку исполнителей.
Совмещение профессий – выполнение одним исполнителем разнотипных работ и функций, при условии, что владеет несколькими специальностями. Это позволяет рационально использовать время и сократить численность занятых рабочих.
На совмещении профессий строится многоагрегатное обслуживание, т.е. поочередное обслуживание одним рабочим или бригадой рабочих нескольких единиц оборудования, при этом ручные работы выполняются во время машинно-автоматной работы оборудования при условии, что не требуется присутствия рабочего.
В зависимости от периода работ и специализированные, и комплексные бригады могут быть сменными и сквозными. Сменные бригады – работа принимается по результатам за смену. Сквозные организуют в том случае, если бригада обслуживает агрегат или выполняет работу, продолжительность которой не равна и не кратна продолжительности смены. И результат работы должен зафиксировать и оценить по истечении нескольких смен работ. Снижается потеря времени на передачу смен.
Разделение и кооперацию труда необходимо производить с количественными и качественными оценками. Научно обоснованные меры затрат труда в конкретных организационно-технических условиях устанавливаются в процессе технического нормирования.
В зависимости от вида и задач производства устанавливают следующие меры затрат труда:
1. Расчетно-техническая норма времени, т.е. регламентированное время выполнения работы в одних и тех же условиях технических и организационных исполнителями одной и той же квалификации. Этот вид широко используется в машиностроении для нормирования труда основных и вспомогательных работах, где могут устанавливать меру затрат труда.
2. норма выработки, т.е. регламентированный объём работ; может быть выражен количеством изделий, изготовленных одним работником или бригадой соответствующей квалификации и в определенных организационно-технических условиях.
3. норма обслуживания. По ней устанавливают количество объектов, которые один работник или бригада должны обслуживать за установленное время в определенных организационно-технических условиях.
4. норма численности – количество работников определенного профессионального состава, необходимое для выполнения конкретных производственных функций, функций управления или для выполнения объёма работ в конкретных организационно-технических условиях.
Последние три вида норм используются на работах по проведению ремонта и технологического характера.
5. норма управляемости – количество рабочих, которые подчинены одному руководителю. В аппарате управления норма управляемости 6 – 7 чел. На 1-го управляющего.
Перечисленные технологические нормы являются основанием для определения численности промышленного производственного персонала.
Классификация затрат рабочего времени.
1. Время работы – состоит из времени подготовки к данной работе.
А). Подготовительно-заключительное время (ПЗВ) учитывается в норме времени в условиях серийности производства.
В состав ПЗВ относятся затраты времени на получение задания, ознакомление с работой, задача работы.
Б). оперативное время которое затрачивается на выполнение технологической операции. В составе ОВ выделяют: основное, вспомогательное. Основное затрачивается на технологическую цель данной работы.
Вспомогательное затрачивается на обеспечение основной работы.
Основное и вспомогательное время может быть машинно-автоматическим (рабочий наблюдает за технологическим процессом), может быть машинно-ручным (процесс идет на оборудование и требуется ручное управление оборудованием), может быть ручным (работы выполняется без помощи оборудования).
В). время работ – время обслуживания рабочего места включает время технического обслуживания рабочего места (смена инструмента) и время организационного обслуживания рабочего места (уборка, чистка, смазка оборудования).
2. Время перерывов: регламентированных и нерегламентированных.
Регламентированные перерывы включают перерывы по организационно-технологическим причинам (несинхронность процесса производства), отдых рабочего (от 2% от первого времени).
Нерегламентированные перерывы состоят из потерь:
- по организационно-техническим причинам (отключение энергии).
- из-за нарушения технологической и трудовой дисциплины рабочих
В состав технологической нормы времени включается:
- подготовительно - запланированное время
- основное время на выполнение операций
- вспомогательное время, если оно не перекрывается с основным
- время обслуживания рабочего места, если оно не перекрывается с основным.
- время регламентированных перерывов.
Все остальное относят к потерям рабочего времени и не нормируется.
Методы нормирования.
Существуют 2 метода:
- аналитические
- суммарные.
Аналитические предполагают деление нормированной операции на элементы, анализ факторов, влияющий на их продолжительность, проектированное рациональной структуры операции и условий ее выполнения, расчет нормы времени.
Аналитические методы нормирования могут быть :
- аналитически-расчетными
- аналитически-исследовательскими.
Расчетные – определяются на основе заранее разработанных нормативов.
Нормативы времени содержат исходные величины для расчета составляющих частей нормы времени, разрабатываются на типовые элементы работы.
Исследовательские – предусматривают проведение наблюдений, хронометражных замеров и фотографии рабочего времени.
Суммарные: опытные и статические.
Опытные - используется опыт нормировщика.
Статические – используются статические наблюдения. И испытание математических моделей. Этот способ широко используется для изготовления норм времени для специалистов.
Цели и задачи управления производством
Непосредственно управление производством осуществляется на основе планирования (целеполагания), организации работ (распорядительства), координации, мотивации труда, контроля за исполнением решений и регулирования хода производства.
Производственные подразделения предприятия действуют и развиваются в соответствии с определенными целями, то есть побуждающими мотивами производства, обуславливающими характер и системную упорядоченность деятельности коллектива и каждого из его членов. Для предприятия в целом характерна основная (стратегическая, глобальная) цель, определяющая направленность его функционирования в соответствии с выбранным или установленным ассортиментом, объемом выпуска и качества продукции. Реализация указанной цели требует четкого определения коллективом подразделений конкретных задач, мероприятий для их выполнения, а также соответствующих ресурсов.
Цели и задачи – это те конечные рубежи, к достижению которых направлена деятельность коллектива цеха. Каждое подразделение может иметь свои задачи. Они должны способствовать достижению целей организации предприятия. Практически цели и задачи являются идентичными по конечным результатам выполнения. Задачу можно представить в качестве конечного результата выполнения производственной программы, а цель – как количественные и качественные показатели работы предприятия, его подразделений. Так, перед мастером производственного участка на текущий месяц можно поставить задачу по выпуску определенного ассортимента, количества, качества и стоимости деталей.
Перед руководителем же предприятия, цеха могут стоять такие цели, как: произвести определенное количество изделий при определенных издержках на их производство, снизить процент брака, не допустить текучести рабочей силы, закупить и установить новое оборудование или осуществить перестановку действующего оборудования к установленному сроку и т.д.Это количественные показатели цели коллектива.
Качественные показатели цели имеют более расплывчатый характер и отражают задачи коллектива в общем виде на определенный период: год, квартал, месяц. К ним можно, например, отнести следующие цели:
o усовершенствовать организационную структуру управления производством в связи с созданием автоматизированных рабочих мест (рабочих станций) специалистов по управлению, экономистов, бухгалтеров;
o осуществить переподготовку кадров функциональных служб предприятия, цехов;
o организовать и укомплектовать аппарат квалифицированными кадрами, чтобы это способствовало повышению эффективности производства и управления;
o установить непроизводственные потери времени рабочих и служащих; и т.д.
Так как в цехах организуется коллективная деятельность работающих, каждая поставленная цель является групповой. В связи с этим важно, чтобы цель была известна каждому работающему в такой форме, которая позволяет проверить ее достижение и тем самым измерять результативность и эффективность работы коллектива.
Процесс управления производством
Процесс управления производством можно представить как совокупность последовательных действий управленческого персонала по определению целей для объектов управления и их фактического состояния на основе регистрации и обработки соответствующей информации, формирование и утверждение (принятие решений) экономически обоснованных производственных программ и оперативных заданий.
Эта последовательность действий управленческого персонала должна осуществляться на основе теоретических положений и разработанных учеными и практиками принципами управления: единоначалие, оптимальное распределение обязанностей, оптимальное число уровней, информационная обеспеченность руководителя, наличие контроля, единство первичной информации, оптимальность информационной нагрузки, заинтересованность исполнителя в результате.
Процесс управления производством будет осуществляться более эффективно, если в управлении предприятием будут использоваться известные принципы управления:
1. Четкое разделение труда, что приводит к появлению высококвалифицированных специалистов.
2. Иерархичность уровней управления, при которой каждый нижестоящий уровень контролируется вышестоящим и подчиняется ему.
3. Наличие взаимосвязанной системы обобщенных формальных правил и стандартов, обеспечивающей скоординированность различных задач и однородность выполнения сотрудниками своих обязанностей.
4. Формальная обезличенность официальных лиц при выполнении ими своих должностных обязанностей.
5. Осуществление найма на работу в строгом соответствии с техническими квалифицированными требованиями. Защищенность служащих от произвольных увольнений.
Цехи основного производства требуют четкой и строгой регламентации их работы, согласованного взаимодействия трудовых коллективов по изготовлению продукции и выполнению целей. Это достигается в результате определения для каждого цеха целей, конкретных задач для реализации целей на основе изучения фактического состояния производства и выработки решений по их практическому выполнению.
Любой цех в каждый плановый период характеризуется определенной производственной ситуацией, которая непосредственно влияет на выполнение поставленной цели. Не учитывать эту ситуацию нельзя.
Поэтому важным фактором в процессе управления является оценка фактического состояния производства в каждом цехе и определение путей преодоления возникших в ходе производства противоречий между целью и сложившейся производственной ситуацией. В соответствии с этим определяются конкретные задачи каждого цеха, которые учитывают максимальные возможности по реализации поставленных целей.
Заключительным этапом процесса управления являются выработка и принятие управленческих решений, в которых устраняются указанные выше противоречия, намечаются пути организационного обеспечения для выполнения задач.
Практическая реализация процесса управления выражается в периодически повторяющихся работах по формированию производственных программ цехам, оперативных сменно-суточных заданий участкам, бригадам и непрерывном слежении за их выполнением.
Первая часть указанных работ относится к планированию производства, которая проводится в соответствии с установленными плановыми периодами (один раз в квартал, месяц, неделю, сутки, смену). Вторая связана с контролем выполнения плановых заданий, со сбором и использованием полученной информации для регулирования хода производства.
Выполнение принятых управленческих решений требует соответствующего организационного обеспечения, которое сопровождается регламентацией работы подразделений, созданием нормативной базы планирования, инструктажем исполнителей, организацией взаимодействия (координацией работы) звеньев и ступеней управления производством.
Указанные выше действия управленческого персонала должны предусматривать определенную меру ответственности руководителей подразделений и их функциональных органов за возможный срыв выполнения производственных программ и заданий. В связи с этим возникает необходимость соблюдения каждым участником производственного процесса строгой дисциплины по своевременному выполнению работ, а также постоянному контролю и регулированию хода производства.
Функции управления производством
В процессе производства между цехами устанавливаются определенные производственные отношения и отношения управления, которые отражают связи между непосредственными производителями продукции, управленческим персоналом, и организацию совместной деятельности участников производства. Конечные цели для предприятия в целом и для каждого цеха определяют направления преобразований отношений производства и управления, и тем самым требования к организационной структуре, организации и процессу управления.
Для реализации указанных воздействий используются рационально распределенные и взаимосвязанные во времени и пространстве функции, методы и организационная структура управления.
Функции управления производством многообразны и затрагивают все его стороны.
Основными (общими) функциями управления производством являются: организация, нормирование, планирование, координация, мотивация, контроль и регулирование.
Функция организации имеет отношение к организации работ по реализации каждой функции управления. Применительно к производственному подразделению предприятия или отдельному цеху функция организации в первую очередь отражает структуру управляемой и управляющей систем, обеспечивающих процесс производства продукции и целенаправленное воздействие на коллектив людей, реализующих этот процесс.
На действующем предприятии совершенствование организации производства сопровождается совершенствованием системы управления.
Организация управления – это совокупность приемов и методов рационального сочетания элементов и звеньев управляющей системы и ее взаимосвязи с управляемым объектом и другими управляющими системами во времени и пространстве.
Функцию нормирования следует рассматривать как процесс разработки научно обоснованных расчетных величин, устанавливающих количественную и качественную оценку различных элементов, используемых в процессе производства и управления. Рассчитываемые по этой функции календарно-плановые нормативы (производственные циклы, размеры партий, заделов деталей и др.) служат основой планирования, определяют продолжительность и порядок движения предметов труда в процессе производства.
Вместе с тем на предприятиях и цехах создаются и действуют нормативы, определяющие технический уровень выпускаемой продукции (стандарты и технические условия), нормативные документы, характеризующие права и обязанности различных звеньев управления, формирующие правила поведения системы в целом (инструкции, методики), и др. В этом понимании нормирование относится к функции организации системы.
Функции организации и нормирования имеют двойственный характер. Так, функция организации характеризует создание (совершенствование) системы управления, а на стадии организации работы реализуется при непосредственном управлении производством. Функция нормирования реализуется с помощью нормативных документов, инструкций при создании системы, а разработанные календарно-плановые нормативы используются при планировании производственной деятельности.
Функция планирования занимает центральное место среди всех функций управления, так как призвана строго регламентировать поведение объекта в процессе реализации поставленных перед ним целей. Она предусматривает определение конкретных задач каждому подразделению на различные плановые периоды и разработку производственных программ.
Разрабатываемые на основе календарно-плановых нормативов движения производства программы выпуска деталей и изделий предусматривают наиболее полное использование передовой техники и технологии, производственной мощности предприятия, материальных и моральных стимулов повышения производительности труда.
Функция координации позволяет добиться согласованной и слаженной работы участвующих в процессе выполнения плановых заданий производственных и функциональных подразделений предприятия и цехов. Эта функция реализуется в форме воздействия на коллектив людей, занятых в процессе производства, со стороны линейных руководителей и функциональных служб предприятия и цехов, которые регулярно и оперативно координируют их деятельность.
Функция мотивации оказывает влияние на коллектив цеха в форме побудительных мотивов к эффективному труду, общественного воздействия, коллективных и личных поощрительных мер и т.д. Указанные формы воздействия активизируют работу органов управления, повышают эффективность всей системы управления производством.
Функция контроля проявляется в форме воздействия на коллектив людей посредством выявления, обобщения, анализа результатов производственной деятельности каждого цеха и доведения их до руководителей подразделений и служб управления с целью подготовки управленческих решений. Эта функция реализуется на основе информации о ходе выполнения плановых заданий (данных оперативного, статистического, бухгалтерского учета), выявления отклонений от установленных показателей работы (контроля исполнения заданий) и анализа причин отклонений.
Функция регулирования непосредственно смыкается с функциями координации и контроля. В ходе производства разработанные программы подвергаются воздействию со стороны внутренней и внешней среды, в результате чего возникают нарушения в процессе выполнения заданий. Функция регулирования воздействует на коллектив людей занятых в производстве, посредством принятия оперативных мер по предотвращению и, если это не удается, то по устранению выявленных отклонений и перебоев в ходе производства. Одновременно происходит координация текущей работы взаимосвязанных звеньев производства для поддержания его ритмичности.
Элементы системы управления производством
В обобщенном виде понятие о системе управления производством можно сформулировать следующим образом. Система управления производством представляет собой совокупность взаимосвязанных структурных элементов (информации, технических средств ее обработки, специалистов, отделов (бюро) по управлению, связей и отношений между ними, соответствующих функций, методов и процессов управления), обеспечивающих при их скоординированном взаимодействии реализацию производственными подразделениями поставленных целей.
В этой системе можно выделить общие элементы. Такими элементами являются: процесс управления, цели системы, объект управления, субъект управления, контур управления и др.
Производство продукции является основным содержанием работы предприятия. Управление этим процессом организуется в масштабе предприятия, в каждом из основных цехов. Содержательной и наиболее ответственной работой по управлению производством является планирование производства изделий. Эта работа регулярно повторяется, выполняется функциональными службами и линейными руководителями производственных подразделений.
Уравленческий персонал отделов (бюро) предприятия и цехов, участвуя в этом процессе, осуществляет регламентацию всей совокупности указанных выше функций, форм и методов управления, использует необходимые рычаги воздействия для поддержания устойчивости производства и стимулирования работы коллектива каждого подразделения в целях выполнения программы и достижения наибольшей эффективности производства.
Разработка производственных программ и выполнение других функций по управлению производством основываются на использовании управленческим персоналом информации целевого назначения о ходе производства, а также средств вычислительной техники для ее обработки. Здесь персонал, информация, вычислительная техника выступают как материальные элементы, используемые в процессе управления. Между этими элементами имеют место определенные связи и отношения управления.
Взаимосвязь элементов системы управления производством представлена на рис.
Организационная структура управления производством
Система управления производством имеет свою структуру. Под структурой управления предприятием понимается упорядоченная совокупность взаимосвязанных элементов, находящихся между собой в устойчивых отношениях, обеспечивающих их функционирование и развитие как единого целого.
Деятельность предприятия и его подразделений должна направляться и координироваться соответствующим руководителем или специальным органом. Чем глубже разделение труда на предприятии и соответственно больше видов деятельности и подразделений, тем сложнее оказывается вся структура органов управления, тем больше в ней уровней иерархии.
Конкретную организационную структуру управления предприятием определяют группы показателей, параметров, факторов, признаков:
Оценочные параметры
Затраты на содержание системы управления
Напряженность труда в подразделениях
Информационная нагрузка на работающих
Время обработки информации
Время реагирования на производственные сбои
Время реагирования на оперативные запросы
Время решения задач управления
Количество ошибок в управленческих решениях
Признаки оптимальной структуры
Небольшие подразделения с высококвалифицированным персоналом
Небольшое число уровней руководства
Наличие в структуре групп специалистов
Ориентация графиков работы на потребителей
Быстрая реакция на изменения
Высокая производительность
Низкие затраты
Итоговые характеристики
Прибыль предприятия
Себестоимость продукции
Организация управления производством
В рамках структуры управления протекает управленческий процесс (движение информации и принятие управленческих решений), между участниками которого распределены задачи и функции управления, а следовательно – права и ответственность за их выполнение. С этих позиций структуру управления можно рассматривать как форму
разделения и кооперации управленческой деятельности, в рамках которой происходит процесс управления, направленный на достижение намеченных целей менеджмента.
В процессе управления функции управления дополняют и проникают друг в друга, в совокупности и взаимосвязи они образуют цикл управления и отражают содержание повседневного управления производством (см. рис. )
Для предприятия в целом свойственны специальные функции (функциональные подсистемы), отражающие конкретное экономическое содержание системы управления. Среди них – подсистема «Управление производством». Функциональные подразделения каждой подсистемы характеризуют организационную структуру управления предприятием, приводящую в соответствие содержание (функции) и форму управления. Каждое из соподчиненных и взаимосвязанных звеньев управляющей системы реализует определенную часть процесса управления.
Для каждого из основных цехов можно выделить четыре основные функциональные подсистемы:
1. Управление экономической деятельностью.
2. Управление технологической подготовкой производства.
3. Оперативное управление производством.
4. Управление техническим обслуживанием производства.
Исполнение каждого управленческого решения осуществляется аппаратом управления. Это заключительная стадия процесса управления, на которой линейными руководителями и функциональными службами в организационно-практической работе используются указанные выше и специфические для каждого цеха методы управления.
Из приведенной характеристики функций управления следует, что каждая из них имеет определенное место и значение в процессе управления, все они взаимосвязаны между собой и дополняют друг друга при выработке управленческих решений.
В современных условиях в руководстве крупным предприятием задействован аппарат управления, поскольку необходимо решать много проблем, в ресурс у каждого работника управления ограничен. Кроме того, проблемы настолько разнообразны и специфичны, что знаний и опыта одного лица недостаточно, чтобы осуществить квалифицированный анализ и найти привлекательное решение.
В связи с этим возникает задача рационального распределения управленческих полномочий и ответственности в рамках структуры управления между ее отдельными уровнями управления и подразделениями.
В соответствии с уровнями менеджмента можно рекомендовать следующее распределение полномочий, ответственности и обязанностей:
Высшие менеджеры
1. Определять цели.
2. Формировать организационную структуру.
3. Распределять стратегические ресурсы.
4. Управлять прибылью.
Менеджеры среднего уровня
1. Давать задания. Планировать. Принимать решения.
2. Подбирать кадры. Обучать персонал.
3. Контролировать и координировать работу.
4. Поддерживать самостоятельность в работе сотрудников.
Менеджеры первого уровня
1. Принимать самостоятельные решения в рамках своей компетенции.
2. Сообщать начальнику, если решение выходит за рамки компетенции.
3. Откровенно высказывать свое мнение.
4. Продумывать возможность улучшения своей деятельности.
5. Информировать руководителя о своей деятельности.
6. Координировать свою деятельность с другими сотрудниками.
7. Повышать свою квалификацию.
Организация управления производством на уровне предприятия осуществляется планово-экономическим и производственно-диспетчерским отделами, связанными с ИВЦ. Специалисты этих подразделений на соответствующих АРМ в диалоге с ЭВМ ИВЦ предприятия организуют разработку производственной программы предприятия, ее экономическое обоснование, распределение по цехам и при необходимости соответствующую корректировку. Этот вид работы относится к функции управления производственной программой предприятия и реализует по существу межцеховое планирование и регулирование производства.
На уровне цехов осуществляется разработка серии производственных программ и заданий для цеха, производственных участков, бригад, т.е. реализуется функция управления производственной программой цеха. Эту работу выполняют специалисты производственного бюро цеха.
Планирование – основная составляющая менеджмента менеджмента.
1. Планирование - базируется на всестороннем анализе ситуации в которой находится предприятие в данный момент. И затем разрабатывается блок плана, который можно считать основным управляющим воздействием на деятельность предприятия.
План стратегического развития, в котором не приводится подробных расчетов, а формируется общая цель и задачи. В этом плане указывается ключевые технико-экономические показатели (уровень прибыли, источники инвестирования. Основные направления по использования новой техники, технологии). Этот план составляется в перспективе на 10 – 15 лет.
- На базе стратегического плана разрабатываются планы тактические. Они также требуют анализ ситуации. Период – 3 – 5 лет. В этих планах в отдельных направлениях развития приводятся более конкретные цифры и расчеты (расходы, доходы, план по персоналу). Далее переход к текущему планированию. Эти планы разрабатываются на 1 год, квартал, месяц. В годовых планах четко выделены разделы:
- План производства
- План инновационной деятельности предприятия
- план по труду, кадрам и заработной платы.
- план по затратам и результатам хозяйственной деятельности предприятия. Планируют численность персонала, уровень оплаты труда.
Содержание текущего планирования
1. План производства – разрабатывается в натуральных показателях, по всей номенклатуре и ассортименту выпускаемой продукции. Затем рассчитывают стоимостные показатели плана: объем товарной продукции, объем валовой продукции, объем реализованной продукции, объем чистой продукции. Стоимостные показатели определяются в плановых ценах (см. курс экономики).
2. План инновационной деятельности предприятия. Может представлять собой свод бизнес-планов: указывать по какому направлению, какая сумма инвестиций требуется, если предприятие ведет КНИСР указывают исполнителей проведения исследований, конструкторских разработок. Указывают сроки выполнения и затраты на их проведение.
3. План по труду, кадрам и зарплате. Указывают численность работающих по категориям и группам профессий. База – план производства и рассчитывается плановый фонд оплаты труда. Рассчитывают фонд оплаты труда (основной зарплаты, дополнительной оплаты за условия труда, надбавки, премии, оплату отпуска). В фонд оплаты труда входят премиальные выплаты средств формируемых за счет прибыли.
Разрабатывают план по затратам:
- материальным;
- трудовым.
На установленный плановый объем производства. Определяют результаты, прибыль (общая и остающаяся в распоряжении предприятия после уплаты налогов). Предусматривается распределение прибыли по направлениям использования на развитие производства, поощрение, социальную сферу, резерв (фонд риска).
Нормативной базой для разработки всех разделов плана служит: нормирование материальных затрат (включая топливо, энергию) и нормативную базу по труду.
На базе годовых планов разработаны планы на месяц. А затем идет блок оперативного планирования по декадам, дням и сменам.
Надо знать фонд оплаты труда и включить его. Надо знать длительность производственного цикла. Деловое планирование (бизнес планы). Бизнес план является основным видом делового планирования связанного с проведением на уже работающих предприятиях работ, связанных с их техническим перевооружением, реконструкцией, обновление выпускаемой продукции, расширением сортамента выпускаемой продукции или расширением продукции. В соответствии с заданными в каждом случае устанавливается период функционирования бизнес плана. Состоит он из нескольких разделов: а) Резюме (помещается вначале, но готовится в конце обработки); указывают в нем цель бизнес планирования, суммы инвестиции необходимы для реализации и показателей инновационного процесса.
1) характеристика предприятия, цель деятельности характеристики предприятия, где будет реализован бизнес-план.
2) Маркетинговые исследования позволяют обосновать необходимость реализации данного бизнес-плана. Приводят анализ цен конкурентов, анализ спроса и предложения, определяют уровень конкурентоспособности продукции после реализации бизнес-плана.
3) План производства строится оп выводам по предыдущему разделу. План проводят в натуральных единицах измерения.
4) Организация управления указывают состав, уровень квалификации, численность персонала, который будет использован в результате реализации бизнес-плана. Определяются средства на оплату труда установленного состава работающих. Определяется средний уровень оплату труда.
5) Затраты на реализацию проекта и текущие. Иногда затраты на реализацию проекта выделяются в отдельный раздел.
6) Экономическая эффективность инвестиционного проекта или бизнес-плана. Расчет экономического эффекта зависит от сроков реализации бизнес-плана.
7) Определение точки безубыточной работы. Установление объема продукции при котором и затраты и результаты одинаковые. Определяют объем работы, который обеспечивает возврат средств в определенный период.