Московский Государственный Технический Университет
им. Н.Э. Баумана
Калужский филиал
Факультет: Конструкторско-механический (КМК)
Кафедра: «Деталей машин и подъемно-транспортного оборудования» К3-КФ
Расчетно-пояснительная записка
к курсовому проекту
по дисциплине: Детали машин
на тему: Привод элеватора
вариант: 13.08
ДМ. 13.08.00.00. ПЗ
________________________________
Калуга 2005г.
Содержание
1. Техническое задание
2. Кинематическая схема механизма
3. Выбор электродвигателя
4. Определение мощности, крутящего момента и частоты вращения для каждого вала
5. Проектный и проверочный расчет конической передачи редуктора
6. Определение диаметров валов
7. Выбор и проверка подшипников качения по динамической грузоподъёмности.
8. Проверочный расчет тихоходного вала (наиболее нагруженного)
9. Выбор и расчёт шпоночных соединений.
10. Расчет цепной передачи
11. Выбор муфт
12. Выбор посадок зубчатых колес, подшипников, звездочек
13. Выбор смазочного материала и способа смазывания зубчатыхзацеплений и подшипников
Литература
1. Техническое задание
2. Кинематическая схема привода
элеватора

1. Электродвигатель
2. Муфта упругая
3. Редуктор
4. Цепная передача
5. Барабан
6. Останов
7. Рама
I. Вал быстроходный
II. Вал тихоходный
III. Вал приводной
Z1
– колесо быстроходное
Z2
– колесо тихоходное
3. Выбор электродвигателя
1. Общий коэффициент полезного действия:
;
nм
=0,98 – КПД муфты;
nред
=0,96 – КПД редуктора;
пц.п.
=0,93 – КПД цепной передачи;
nподш
=0,99 – КПД опоры вала

2. Мощность электродвигателя:
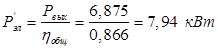
где Р΄эл
– предварительная мощность э/д, [кВт];
Рвых
– мощность на выходе, [кВт];

где Ft
= 2750 Н – окружное усилие на барабане;
v = 2,5 м/с – скорость ленты транспортёра;
По таблице определяем, что Рэл
= 11кВт.
3. Частота вращения приводного вала:
,
где n3
– частота вращения приводного вала [мин-1
];
Dб
= 375 мм – диаметр барабана;
Рассмотрим возможные варианты передаточных чисел редуктора
– общее передаточное число;
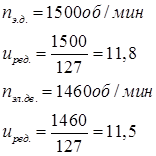
,
Принимаем ;
;
где - передаточное число цепной передачи;
- передаточное число редуктора;
Воспользуемся [1], где по таблице 24.8 выбираем электродвигатель 4A132М4, который имеет следующие параметры:
Рэ.д.
= 11 кВт, nэ.д.
= 1460 мин-1
.
Определим мощности: ;
;
;
где – мощность на валах редуктора, быстроходного, тихоходного валов и приводного вала, – коэффициенты полезного действия муфты, редуктора, цепной передачи и опор соответственно.
Определим частоту вращения: ;
;
;
где – частота вращения на валах редуктора, быстроходного, тихоходного валов и приводном вале.
Определим крутящие моменты: ;
;
;
где – крутящие моменты на валах редуктора быстроходного, тихоходного и приводного валов.
Результаты расчётов занесём в таблицу 1.
Таблица 1.
Вал |
Мощность  |
Частота вращения  |
Крутящий момент  |
1 |
10,78 |
1460 |
70,5 |
2 |
10,35 |
365 |
270,8 |
3 |
9,53 |
127 |
716,625 |
5. Проектный и проверочный расчет конической передачи редуктора
Материал колеса и шестерни – сталь 40Х. Таким образом, учитывая, что термообработка зубчатых колёс и шестерни – улучшение, имеем:
для шестерни
: ;
для колеса
: ;
где – предел текучести материала.
Определим среднюю твёрдость зубьев шестерни и колеса:
;

где – твёрдость рабочей поверхности зубьев.
Определим коэффициенты приведения на контактную выносливость и на изгибную выносливость по таблице 4.1., учитывая режим работы №3: ; .
Определим число циклов перемены напряжений.
Числа циклов перемены напряжений соответствуют длительному пределу выносливости. По графику 4.3. определяем числа циклов на контактную и изгибную выносливость соответственно:
, , .
Найдём ресурс передачи, т.е. суммарное время работы:
,
где – срок службы передачи, годы; – коэффициент использования передачи в течение года; – коэффициент использования передачи в течение суток.
Определим суммарное число циклов перемены напряжений для шестерни и колеса соответственно:
,
,
где – ресурс передачи; и – частота вращения шестерни и колеса соответственно; = = 1 – число вхождений в зацепление зубьев шестерни или колеса соответственно за один его оборот.
Определим эквивалентное число циклов перемены напряжений для расчёта на контактную выносливость:
,
,
где – коэффициенты приведения на контактную выносливость; – суммарное число циклов перемены напряжений для шестерни или колеса.
Так как , то принимаем и
, то .
Определим эквивалентное число циклов перемены напряжений для расчёта на изгибную выносливость:
,
,
где – коэффициенты приведения на изгибную выносливость; – суммарное число циклов перемены напряжений для шестерни или колеса.
Так как и , то принимаем .
Определим допускаемые напряжения для расчётов на выносливость. По таблице 4.3 находим
для шестерни
:
,

, 
для зубчатого колеса
:
, ,
, ,
где и – длительный предел контактной выносливости и коэффициент безопасности; и – длительный предел изгибной выносливости и коэффициент безопасности; – средняя твёрдость зубьев шестерни или колеса.
Определим предельные допускаемые контактные и изгибные напряжения:



,
где – предел текучести материала колеса или шестерни.
Проверим передачу на контактную выносливость:
, , , .
Принимаем допускаемое контактное напряжение как меньшее значение:
.
Определим коэффициенты нагрузки на контактную и изгибную выносливость по формулам:
и ,
где и – коэффициенты концентрации нагрузки по ширине зубчатого венца; и – коэффициенты динамической нагрузки (учитывают внутреннюю динамику передачи).
Относительная ширина зубчатого венца находится по формуле
,
где =4 – передаточное число редуктора.
По таблице 5.2. и 5.3, схемы 2 расположения зубчатых колёс относительно опор и варианта соотношения термических обработок “a” находим , 
Тогда


Значения определяются по табл. 5.6 по известной окружной скорости:
,
где = 1460 м/с – частота вращения быстроходного вала,
=270,8 – крутящий момент на валу,
=4 – передаточное число редуктора,
коэффициент определяется по табл. 5.4 в зависимости от вида передачи.
Принимаем 8-ю степень точности изготовления передачи находим, что
и .
Теперь находим значения коэффициентов нагрузки


Определим предварительное значение диаметра внешней делительной окружности колеса d΄e
2
:
,
где – коэффициент вида конических колёс

Из стандартного ряда выбираем по ГОСТ 12289-66 ближайшее стандартное значение диаметра внешней делительной окружности 
Определяем предварительное значение диаметра внешней делительной окружности шестерни d'е1
:
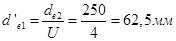
Вычислим число зубьев шестерни Z1
, учитывая, что минимальное число зубьев для передачи :
По графику находим Z'1
= 12, учитывая таблицу .
Принимаем Z1
= 19
Вычислим число зубьев колеса Z2
:
.
Найдём окончательное значение передаточного числа:
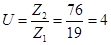
Определяем углы делительных конусов δ:
δ2
= arctg(U) = arctg (4) = 75,964°
δ1
= 90 - arctg(U) = 90 - arctg (4) = 14,036°
Определяем внешний окружной модуль mte
:
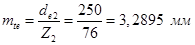
Определяем внешнее конусное расстояние Re
:

Вычисляем рабочую ширину зубчатого колеса b:
.
Принимаем b = 37мм.
Определяем коэффициент смещения инструмента Xn
:
По таблице 7.5. для шестерни Xn
1
= 0.305, для колеса Xn
2
= - 0.305.
Проверим зубья колёс на изгибную выносливость. Для колеса получим:

где YF
2
= 3.63 – коэффициент учитывающий форму зубьев колеса. Определяется по табл. 6.2, при коэффициенте смещения Xn
2
= - 0.305 и биэквивалентным числе зубьев .
- коэффициент вида конических колёс. Определяется по формуле

Сравниваем полученное значение напряжения с допускаемым напряжением при расчёте на изгиб зубьев:
колеса:
.
шестерни
:
,
где и – коэффициенты, учитывающие форму зуба, определяются по табл. 6.2 лит. 1.
Сравним полученное значение напряжения с допускаемым напряжением при расчёте на изгиб зубьев шестерни:
.
Определяем окончательное значение диаметра внешней делительной окружности:

Определяем внешние диаметры вершин зубьев:
шестерни

колеса

Определяем средний нормальный модуль:

Выполним проверку возможности обеспечения принятых механических характеристик при данной термической обработке заготовки (термическое улучшение).
Для колеса
:
, – верно,
здесь – наибольший размер сечения заготовки. Для шестерни: , – верно, где – наибольший размер сечения заготовки.
Определим силы, действующие на валы зубчатых колёс.
Окружную силу на среднем находим по формуле:
,
где .
Осевая сила на шестерне:
,
где 
Радиальная сила на шестерне:
,
где 
Осевая сила на колесе:
Н
Радиальная сила на колесе:
Н
Диаметры различных участков валов редуктора определим по формулам:
А) для тихоходного вала
Определим диаметр тихоходного вала:
. Принимаем 
Для найденного диаметра вала выбираем значения: – приблизительная высота буртика, – максимальный радиус фаски подшипника, – размер фасок вала.
Определим диаметр посадочной поверхности подшипника:
. Принимаем 
Рассчитаем диаметр буртика для упора подшипника:
. Принимаем 
Б) для быстроходного вала
Определим диаметр быстроходного вала шестерни:
. Принимаем 
Для найденного диаметра вала выбираем значения: – приблизительная высота буртика, – максимальный радиус фаски подшипника, – размер фасок вала.
Определим диаметр посадочной поверхности подшипника:
. Принимаем 
Рассчитаем диаметр буртика для упора подшипника:
. Принимаем 
I. Для быстроходного вала редуктора выберем роликоподшипники конические однорядные средней серии . Для него имеем: – диаметр внутреннего кольца, – диаметр наружного кольца, – ширина подшипника, – динамическая грузоподъёмность, – статическая грузоподъёмность, – предельная частота вращения при жидкой смазке. На подшипник действуют: – осевая сила, – радиальная сила. Частота оборотов . Требуемый ресурс работы , , при Fa
/VFr
> e.
Найдём: – коэффициент безопасности (табл. 1 лит. 2); – температурный коэффициент (стр. 12 лит. 2); – коэффициент вращения (стр. 10 лит. 2).
Определяем радиальные силы действующие в подшипниках:


Определяем минимальные осевые нагрузки для подшипников:
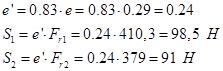
Определяем осевые реакции в опорах:
Принимаем, что Fа1
= S1
= 98,5 Н, тогда из условия равновесия , что больше, чем S2
. Следовательно, силы найдены правильно.
Определяем эквивалентную нагрузку для 1ой
опоры: . Следовательно, X = 1, Y = 0.
Отсюда 
Определяем эквивалентную нагрузку для 2ой
опоры:
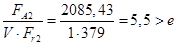
Определяем значение коэффициента радиальной динамической нагрузки и коэффициента осевой динамической нагрузки .
Определяем эквивалентную радиальную динамическую нагрузку .
Рассчитаем ресурс принятых подшипников, (расчет выполняется по 2ой
более нагруженной опоре): , или , что удовлетворяет требованиям.
II. Для тихоходного вала редуктора выберем роликоподшипники конические однорядные средней серии . Для него имеем: – диаметр внутреннего кольца, – диаметр наружного кольца, – ширина подшипника, – динамическая грузоподъёмность, – статическая грузоподъёмность, – предельная частота вращения при пластичной смазке. На подшипник действуют: – осевая сила, – радиальная сила. Частота оборотов . Требуемый ресурс работы , , Y = 1,94 при Fa
/VFr
> e.
Найдём: – коэффициент безопасности; – температурный коэффициент; – коэффициент вращения.

Определяем радиальные силы действующие в подшипниках:

Определяем минимальные осевые нагрузки для подшипников:
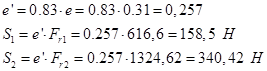
Определяем осевые реакции в опорах:
Принимаем, что Fа1
= S1
= 158,5 Н, тогда из условия равновесия , что больше, чем S2
. Следовательно, силы найдены правильно.
Определяем эквивалентную нагрузку для 1ой
опоры: . Следовательно, X = 1, Y = 0.
Отсюда 
Определяем эквивалентную нагрузку для 2ой
опоры:
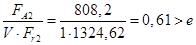
Определяем значение коэффициента радиальной динамической нагрузки и коэффициента осевой динамической нагрузки .
Определяем эквивалентную радиальную динамическую нагрузку .
Рассчитаем ресурс принятых подшипников, (расчет выполняется по 2ой
более нагруженной опоре): , или , что удовлетворяет требованиям.
8. Проверочный расчет тихоходного вала (наиболее нагруженного)
Действующие силы:
– окружная,
– осевая,
– радиальная,
– крутящий момент.
,
,
,
.

Изгибающие моменты в опасном сечении:
от ,
от ,
от ,
Суммарный изгибающий момент будет вычисляться по формуле
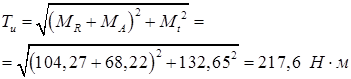
Расчёт производим в форме проверки коэффициента запаса прочности , значение которого можно принять . При этом должно выполняться условие, что , где – расчётный коэффициент запаса прочности, и – коэффициенты запаса по нормальным и касательным напряжениям, которые определим ниже.
Определим механические характеристики материала вала (Сталь 45) по табл. 10.2 лит. [1]: – временное сопротивление (предел прочности при растяжении); и – пределы выносливости гладких образцов при симметричном цикле изгиба и кручении; – коэффициент чувствительности материала к асимметрии цикла напряжений.
Определим отношение следующих величин (табл. 10.3 и 10.6 лит. [1]): , , где и – эффективные коэффициенты концентрации напряжений, – коэффициент влияния абсолютных размеров поперечного сечения. Также по табл. 10.4 лит. [1] найдём значение коэффициента влияния шероховатости и по табл. 10.5 лит. [1] коэффициент влияния поверхностного упрочнения .
Вычислим значения коэффициентов концентрации напряжений и для данного сечения вала: , .
Определим пределы выносливости вала в рассматриваемом сечении: , .
Рассчитаем осевой и полярный моменты сопротивления сечения вала: , где – расчётный диаметр вала.
Вычислим изгибное и касательное напряжение в опасном сечении по формулам: , .
Определим коэффициент запаса прочности по нормальным напряжениям: .
Для нахождения коэффициента запаса прочности по касательным напряжениям определим следующие величины. Коэффициент влияния асимметрии цикла напряжений для данного сечения . Среднее напряжение цикла . Вычислим коэффициент запаса .
Найдём расчётное значение коэффициента запаса прочности и сравним его с допускаемым: – условие выполняется.
9. Выбор и расчёт шпоночных соединений
В данном редукторе шпоночные соединения выполнены с использованием призматических шпонок. Соединение с такими шпонками напряженное, оно требует изготовления вала с большой точностью. Момент передается с вала ступиц узкими боковыми гранями шпонки. При этом возникают напряжения сечения σсм
, а в продольном сечении шпонки напряжение среза τ.
У стандартных шпонок размеры b и h подобранны так, что нагрузку соединения ограничивают не напряжение среза, а напряжение смятия. Поэтому расчет шпонок проведем на напряжение смятия.
1). Соединение быстроходного вала с муфтой.
Имеем:
– крутящий момент на валу,
– диаметр вала,
– длина шпонки,
– ширина шпонки,
– высота шпонки,
– глубина паза вала,
– рабочая длина шпонки,
– допускаемое напряжение на смятие материала шпонки.
Условие прочности: ,
– верно.
2). Соединение тихоходного вала с зубчатым колесом.
– крутящий момент на валу,
– диаметр вала,
– длина шпонки,
– её ширина,
– высота шпонки,
– глубина паза вала,
– рабочая длина шпонки,
– допускаемое напряжение на смятие материала шпонки.
Условие прочности: ,
– верно.
3). Соединение тихоходного вала со звёздочкой.
Имеем:
– крутящий момент на валу,
– диаметр вала,
– длина шпонки,
– её ширина,
– высота шпонки,
– глубина паза вала,
– рабочая длина шпонки,
– допускаемое напряжение на смятие материала шпонки.
Условие прочности: ,
– верно.
– крутящий момент на валу
- часта вращения ведущей звездочки;
U=2,875 – передаточное число цепной передачи.
Привод работает в одну смену; ожидаемый наклон передачи к горизонту около 500
.
1. Назначим однорядную роликовую цепь типа ПР.
2. Предварительное значение шага для однорядной цепи

Ближайшее значение шага однорядной цепи по стандарту: P=31,75 мм ;
А=262 мм2
- площадь проекции опорной поверхности шарнира цепи.
3. Число зубьев ведущей звёздочки
Найдем рекомендуемое число зубьев z1
в зависимости от передаточного числа:

Принимаем 
4.Определим давление в шарнире
кд
=1,2 – нагрузка без ударов и толчков;
кQ
=1 – оптимальное межосевое расстояние;
кн
=1 – наклон передачи менее 600
;
крег
=1,25 – передача с нерегулируемым натяжением цепи;
ксмаз
=1,5 – смазывание цепи нерегулярное;
креж
=1 – работа в одну смену;

Окружная сила передаваемая цепью

Давление в шарнире однорядной цепи

Для дальнейших расчетов принимаем двухрядную цепь 2ПР-25,4-11340.
5. Число зубьев ведомой звездочки
z2
=U·z1
=2,875·23=66,125. Принимаем z2
=66.
6. Частота вращения ведомой звёздочки:
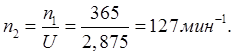
7. Делительный диаметр ведущей звездочки:
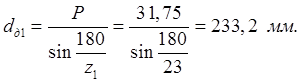
8. Диаметр окружности выступов ведущей звездочки:

9. Делительный диаметр ведомой звездочки:
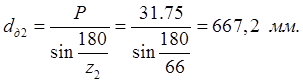
10. Диаметр окружности выступов ведомой звездочки:

11. Диаметр обода ведущей звездочки (наибольший)

12. Диаметр обода ведомой звездочки (наибольший)

Принимаем 
13. Ширина зуба звездочки

14. Ширина венца зуба звездочки

15. Межосевое расстояние
мм.
16. Потребное число звеньев цепи

Принимаем 
17. Уточнение межосевого расстояния
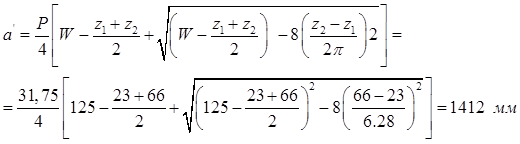
Полученное значение уменьшаем на:

Окончательное значение межосевого расстояния:

18. Нагрузка на валы звездочек:

11. Выбор муфт
Для передачи крутящего момента от вала электродвигателя к быстроходному валу и предотвращения перекоса вала выбираем муфту. Наиболее подходит комбинированная муфта которая состоит из зубчатой и муфты с разрушающимися элементами, крутящий момент передается пальцами и упругими втулками. Ее размеры стандартизированы и зависят от величины крутящего момента и диаметра вала.
12. Выбор посадок зубчатых колес, подшипников, звездочек
Стандарт СЭВ рекомендует применять преимущественно посадки в системе отверстия и в шестерни в системе вала. Применение системы отверстий предпочтительнее, поскольку при этом сокращается номенклатура дорогих инструментов (калибров) для отверстия. Систему вала применяют при технологической целесообразности использования гладких валов, сопряженных с деталями, имеющими различные пределы отклонения.
По рекомендациям примем следующие посадки подшипников:
- для наружных колец H7/l6
- для внутренних колец L5/k6
Для установления шпонки в паз вала воспользуемся рекомендуемой СТ СЭВ 57-73 переходной посадкой P9/h9, а для установки шпонок крепления звездочек и зубчатого колеса воспользуемся соответственно посадками с зазором H9/h9, Js9/h9.
13. Выбор смазочного материала и способа смазывания зубчатых зацеплений и подшипников
Смазочные материалы в машинах применяют с целью уменьшения интенсивности изнашивания, снижения сил трения, отвода от трущихся поверхностей теплоты, а также для предохранения деталей от коррозии. Снижение сил трения благодаря смазке обеспечивает повышение КПД машины, кроме того снижаются динамические нагрузки, увеличивается плавность и точность работы машины
Для смазывания передачи применена картерная система. В корпус заливают масло так, чтобы венцы колес были в него погружены.
Определим окружную скорость вершин зубьев тихоходного колеса:
,
где – частота вращения тихоходного вала,
– диаметр окружности вершин колеса;
Выберем марку масла в соответствии с окружной скоростью колеса и по контактному напряжению: И-Г-А-32. Его кинематическая вязкость для зубчатых колёс при температуре  .
Смазывание подшипников происходит тем же маслом за счёт разбрызгивания. При сборке редуктора подшипники необходимо предварительно промаслить.
Литература
1. П.Ф. Дунаев, О.П. Леликов, “Конструирование узлов и деталей машин”, Москва, “Высшая школа”, 1985 г.
2. Д.Н. Решетов, “Детали машин”, Москва, “Машиностроение”, 1989 г.
3. М.Н. Иванов. Детали машин. М.: «Машиностроение», 1991.
4. В.И. Анурьев – Справочник коструктора –машиностроителя, т.1. М.: «Машиностроение», 1980.
5. В.И. Анурьев – Справочник коструктора –машиностроителя, т.2. М.: «Машиностроение», 1980.
6. В.И. Анурьев – Справочник коструктора –машиностроителя, т.3. М.: «Машиностроение», 1980.
7. С.А. Чернавский и др. Курсовое проектирование деталей машин. М.: «Машиностроение», 1987.
8. Д.Н. Решетов – Детали машин. Атлас конструкций. М.: «Машиностроение», 1970.М.И.
9. Анфимов – Редукторы. Конструкции и расчет. М.: «Машиностроение», 1972.
|