Теория механизмов и машин
Основные понятия и определения.
Теория механизмов и машин занимается исследованием и разработкой высокопроизводительных механизмов и машин.
Механизм совокупность подвижных материальных тел, одно из которых закреплено, а все остальные совершают вполне определенные движения, относительно неподвижного материального тела.
Звенья материальные тела, из которых состоит механизм.
Стойка неподвижное звено.
Стойка изображается ; конфигурация стойки в курсе ТММ не изучается. Звено, к которому изначально сообщается движение, называется входным (начальным, ведущим). Звено, совершающее движение, для выполнения которого предназначен механизм выходное звено.
Кривошипно-
ползунный
механизм
Рис.1
Если это компрессор, то зв.1 входное, а зв.3 выходное.
Если это механизм ДВС, то зв.3 входное, а зв.1 выходное.
Кинематическая пара подвижное соединение звеньев, допускающее их относительное движение. Все кинематические пары на схеме обозначают буквами латинского алфавита, например A, B, C и т.д.
Если , то К.П. вращательная ; если , то поступательная.
Порядок нумерации звеньев:
входное звено 1;
стойка последний номер.
Звенья бывают:
- простые состоят из одной детали;
- сложные состоят из нескольких, жестко скрепленных друг с другом и совершающих одно и тоже движение.
Например, шатунная группа механизма ДВС.
Звенья, соединяясь друг с другом, образуют кинематические цепи, которые разделяют на:
- простые и сложные;
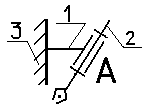
замкнутые и разомкнутые;
Пример замкнутой кинематической
цепи на рис.1;
пример разомкнутой цепи:
Машина техническое устройство, в результате осуществления технологического процесса определенного рода, можно автоматизировать или механизировать труд человека.
Машины условно можно разделить на виды:
- энергетические;
- технологические;
- транспортные;
- информационные.
Энергетические машины разделяют на:
- двигатели;
- трансформирующие машины.
Двигатель техническое устройство, преобразующее один вид энергии в другой. Например, ДВС.
Трансформаторная машина техническое устройство, потребляющее энергию извне и совершающее полезную работу. Например, насосы, станки, прессы.
Техническое объединение двигателя и технологической (рабочей машины) Машинный агрегат (МА).
Внешняя Технологический среда процесс
Двигатель имеет определенную механическую характеристику, рабочая машина тоже. Механические характеристики указаны в техпаспорте.
1 скорость, с которой вращается вал двигателя;
2 скорость, с которой будет вращаться главный вал рабочей машины.
1 и 2 нужно поставить в соответствие друг другу.
Например, число оборотов n1 =7000 об/мин., а n2=70 об/мин.
Чтобы привести в соответствие механические характеристики двигателя и рабочей машины, между ними устанавливают передаточный механизм, который имеет свои механические характеристики.
up2=1/2=700/70=10
В качестве передаточного механизма могут быть использованы:
- фрикционные передачи (с использованием трения);
- цепные передачи (привод мотоцикла);
- зубчатые передачи.
В качестве рабочей машины наиболее часто используют рычажные механизмы.
Основные виды рычажных механизмов.
1. Кривошипно-ползунный механизм.
а) центральный (рис.1);
б) внеосный (дезоксиальный) (рис.2);
е - эксцентриситет
Рис. 2
1-кривошип, т.к. звено совершает полный оборот вокруг своей оси;
2-шатун, не связан со стойкой, совершает плоское движение;
3-ползун (поршень), совершает поступательное движение;
4-стойка.
2. Четырехшарнирный механизм.
Звенья 1,3 могут быть кривошипами.
Если зв.1,3 кривошипы, то механизм двукривошипный.
Если зв.1 кривошип (совершает полный оборот), а зв.3 коромысло (совершает неполный оборот), то механизм кривошипно-коромысловый.
Если зв.1,3 коромысла, то механизм двукоромысловый.
3. Кулисный механизм.
1 - кривошип;
2 - камень кулисы (втулка) вместе с зв.1 совершает полный оборот вокруг А (1 и 2 одно и тоже), а также движется вдоль зв.3, приводя его во вращение;
3 - коромысло (кулиса).
на зв.3 выбирают точку В3 и выбирают в данный момент так, чтобы она совпадала с точкой В.
4.Гидроцилиндр
(в кинематическом отношении подобен кулисному механизму).
В процессе проектирования конструктор решает две задачи:
- анализа (исследует готовый механизм);
- синтеза (проектируется новый механизм по требуемым параметрам);
Анализ рычажных механизмов.
В данной главе будут рассмотрены вопросы:
1. структурный анализ механизма (изучение строения механизма);
2. изучение классов и видов кинематических пар.
3. определение числа степеней свободы механизма и определение наличия или отсутствия избыточных связей; в случае наличия дать рекомендации по способу их устранения;
4. кинематический анализ механизма.
Структурный анализ механизма.
Примечание:
Кинематическая пара существует, если не происходит деформации звеньев, образующих эту пару, и не должно происходить отрыва звеньев одно от другого, образующих кинематическую пару.
Примечание:
Ограничения, накладываемые на независимые движения звеньев, образующих кинематическую пару, называются условия связи S.
Число степеней свободы механизма
W=S+H,
где Н подвижность.
Любое незакрепленное тело в пространстве имеет 6 степеней свободы, на плоскости 3.
Классификация кинематических пар проводят либо числу связей, либо по числу подвижностей:
Число связей Класс КП Число подвижностей
S=1 PI H=5
S=2 PII H=4
S=3 PIII H=3
S=4 PIV H=2
S=5 PV H=1
Существует 5 классов кинематических пар.
Примеры различных КП смотри рис. 4-95.
Кинематические пары по характеру контакта звеньев, образующих КП, разделяют на:
- низшие:
- вращательные;
- поступательные;
- высшие.
Контакт звеньев в низшей КП осуществляется по поверхности. Контакт звеньев в высшей КП либо по линии, либо в точке.
§1.2 Определение числа степеней свободы рычажных механизмов.
1.2.1 Плоские механизмы.
В плоском механизме все звенья движутся в одной плоскости, все оси параллельны друг другу и перпендикулярны плоскости механизма.
ФОРМУЛА ЧЕБЫШЕВА : Wпп=3n -2pн -pв,
Где n число подвижных звеньев механизма, рн число низших КП, рв число высших КП.
n=3
pн=4
рв=0
W=3.3-2.2=1
Рис.1.2.1
Пространственные механизмы.
В пространственном механизме оси непараллельны, звенья могут двигаться в разных плоскостях.
Wпр= 6n - (S1+ S2+ S3+ S4+ S5)
Допустим, что механизм, изображенный на рис.1.2.1 пространственный и все кинематические пары 5-го класса, т.е. одноподвижны AV,BV,CV,DV, тогда
Wпр= 6n - (5pV+4pIV+3pIII+2pII+pI)
Wпр= 6.3 - 5.4 = -2 статически неопределимая ферма.
Для получения Wдейств=0, необходимо добавить 3 движения.
q= Wдейств - Wпр = 1 - (-2) = 3,
где q избыточные связи.
Для того чтобы их устранить, надо изменить класс некоторых кинематических пар, при этом нельзя изменять класс КП А. Поэтому, сделаем КП В сферическим шарниром, т.е. 3-го класса (добавим 2 подвижности), а КП С 4-го класса (добавим 1 подвижность). Тогда
Wпр= 6.3 - ( 5.2 + 4.1 + 3.1 ) = 18 - 17 = 1
n
ФОРМУЛА СОМОВА-МАЛЫШЕВА: Wпр= 6.n - Si + q
i=1
Кинематический анализ рычажных механизмов.
Основные понятия и определения.
Зависимость линейных координат в какой-либо точке механизма от обобщенной координаты линейная функция положения данной точки в проекциях на соответствующие оси координат.
Хс= f(1)
Зависимость угловой координаты какого-либо звена механизма от обобщенной координаты угловая функция положения данного звена.
2= f(1)
Первая производная линейной функции положения точки по обобщенной координате линейная передаточная функция данной точки в проекциях на соответствующие оси координат (иногда называют «аналог линейной скорости…»)
полная скорость т. С будет
Первая производная угловой функции положения звена по обобщенной координате передаточное отношение.
Вторая производная линейной функции положения по обобщенной координате аналог линейного ускорения точки в проекциях на соответствующие оси.
Вторая производная угловой функции положения звена по обобщенной координате аналог углового ускорения звена.
Основными задачами кинематического исследования движения звеньев механизма являются:
1) определение положения звеньев и траекторий заданных точек;
2) определение линейных и угловых скоростей и ускорений звеньев и отдельных точек механизма.
Для этой цели применяются следующие методы:
a) графический (планы скоростей и ускорений);
б) графоаналитический (метод диаграмм);
в) аналитический.
Методы а и б уступают в точности аналитическому, но обладают простотой и наглядностью.
Для выполнения анализа движения звеньев механизма должны быть заданы:
а) схема механизма и
б) размеры его звеньев, а так же
в) функция зависимости перемещений ведущих звеньев от параметра времени или др. параметров их движения.
Построение планов механизма имеет целью определение относительных расположений звеньев и траекторий движения их точек по заданным положениям ведущих звеньев. Решение этой задачи производится при помощи метода засечек.
Планом механизма называют масштаб графического изображения кинематической схемы соответствующей заданному положению входного звена.
Рис 1.
Определение скоростей и ускорений методом построения кинематических диаграмм.
Кинематической диаграммой принято называть зависимость какого-либо параметра движения звена от времени или параметра перемещения ведущего звена, представляемую графически кривой в прямоугольной системе координат.
Наивысший интерес представляют графики S, V, W ведомых звеньев. В качестве параметра S ведущего звена могут быть выбраны либо угол поворота, либо одна из координат принадлежащей ему точки. Эти параметры связаны с параметром времени.
Как известно, функции S,V и W движения какой-либо точки могут быть определены при помощи дифференцирования или интегрирования.
1.Построение диаграммы перемещения.
Строим 12 положений (см.рис.1)
За начало отсчета принимаем положение поршня Во.
Затем выбрав систему координат sb ,t по оси абсцисс откладываем отрезок L(мм) соответствующий времени Т одного оборота кривошипа.
Откладываем Y1= kBoB1; Y2=kВоВ2 и т.д., где BoB1; BoB2 и т.д. отрезки, отражающие перемещения т.В на планах механизма.
k-коэффициент кратности ординат графика Sв=Sв(t) и
Рис.2
отрезков изображающих перемещения BoB1, BoB2 т.В на планах механизма.
Между масштабом плана механизма и масштабом ординат диаграммы перемещений существует зависимость:
s= |
1k |
*e |
Масштаб времени, откладываемого по оси абсцисс:
t= |
T L |
(сек./мин.) |
где Т - время одного оборота ведущего звена в секундах. Если число оборотов кривошипа =n (об/мин), то
T= |
60 n |
(сек) при этом |
t= |
60 nT |
(сек./мин.) |
Аналогично строится график угловых перемещений звена совершающее вращательное движение. В этом случае по оси ординат откладываются отрезки пропорциональные величинам угловых перемещений.
Построение графиков скорости и ускорения по графику перемещения.
Построение графиков V=V(t) и a=a(t) по графику S=S(t) осуществляется методом графического дифференцирования, сущность которого заключается в следующем.
Пусть есть перемещение некоторой точки за малый промежуток времени. Проведем секущую ВС, а из полюса Р, выбранного произвольно на расстоянии Н от начала координат луч, параллельный ВС. Из подобия РАО и ВОД следует:
OA H |
= |
CD BD |
OA= |
CD BD |
*H |
(1) |
Действительное значение перемещения за время отображается отрезком:
CD= |
S s |
отрезок оси абсцисс |
а1 а2 = |
BD= |
t t |
-отображает длительность интервала времени в масштабе. |
Подставив эти значения CD и BD в равенство (1) найдем:
OA= |
S t |
* |
t s |
*H |
(2) |
отношение представляет среднее значение скорости движения точки на пути длинной S, то следует:
Vср= |
ОА* |
s t* H |
(3) |
Если принять масштаб скорости |
V= |
s t* H |
то из равенства (3) отрезок ОА |
отображает величину средней скорости движения точки.
Допуская некоторую погрешность, считают, что это среднее значение скорости соответствует среднему мгновению промежутка t, т.е. точке F.
При изложенном способе дуга ВС заменилась хордой ВС. Допустима также замена дуги соответствующим отрезком касательной. В обоих случаях результаты получаются с погрешностью.
(Рассмотрим на примере рис.2)
График ускорения строится аналогично, путем дифференцирования графика V. При этом новое полюсное расстояние H1H
Определение масштаба графика a получаем, заменив величину sV а вместо HH1
a= |
V t*H1 |
Вследствии двукратного дифференцирования, диаграммы a могут получиться со значительными искажениями.
Поэтому рассмотрим другой способ определения скоростей и ускорений.
Метод планов скоростей и ускорении базируется на теоремах о скольжении векторов скоростей и ускорений, доказываемых в курсах теоретической механики.
Теорема 1 Вектор скорости абсолютного движения точки (Va) равен сумме
векторов скоростей переносного (Ve) и относительного (Vr) движений.
эта теорема была известна еще Архимеду (287-212 гг.д.н.э.)
Теорема 2 (Кориолиса) Вектор ускорения (аn) абсолютного движения материальной точки равен сумме векторов ускорений переносного (ае) и
относительного движений (аr) и ускорения Кориолиса (ac):
Метод планов скоростей и ускорений.
VВАВА
VВо=0 VВво x-x
Все точки координатной системы движутся с одинаковой скоростью. После того, как найдены скорости шарнирных точек механизма, скорости других точек определяем с помощью теоремы подобия:
все жесткие фигуры на плане механизма подобны одноименным фигурам на плане скоростей, а их сходственные стороны взаимно перпендикулярны.
АКВ акв
Планы ускооений
-теорема о сложении ускорений, когда переносное ускорение по форме поступательное.
о
аВ x-x
Для определения ускорения остальных точек используем теорему подобия: все неизменяемые фигуры на плане механизма подобны одноименным фигурам на плане усковений.
Методом засечек получим две точки, одна из них ложная, чтобы найти истинную точку, применяют правило обхода вершин:
порядок чтения вершин при обходе подобных контуров в какую-либо, но одну и ту же сторону, не должен изменяться.
Определение угловых скоростей и угловых ускорений звеньев механизмов
- направление по скорости с плана скоростей в ту же сторону
- направление по тангенциальному ускорению
Шатун АВ вращается ускоренно, т.к. 2 и 2 направлены в одну сторону. Если и направлены в разные стороны, то ползун движется замедленно.
Механизмы с высшей кинематической парой.
В этом разделе будут рассмотрены передаточные механизмы с высшей КП, а именно:
- цилиндрические зубчатые передачи с эвольвентным профилем зубов и постоянным передаточным отношением;
- планетарные механизмы с подвижными осями зубчатых колес.
Достоинство механизмов с высшей КП:
- малые габариты и вес;
- возможность точного воспроизведения закона движения выходного звена (по сравнению с рычажными механизмами зубчатые передачи имеют меньше зазоров);
- высокий КПД (0,85 зубчатая передача, 0,99 планетарный механизм).
Недостатки:
наличие высшей КП может привести к повышенным удельным давлениям в точке контакта. Это в свою очередь может привести к выкрашиванию материалов (питтинг).
Условие существования высшей КП.
Для того чтобы не было отрыва или внедрения поверхностей звеньев, образующих высшую КП, необходимо, чтобы проекции линейных скоростей взаимодействующих тел на общую нормаль, проведенную в точке контакта тел, были равны.
Кинематика высшей КП.
Для определения мгновенного центра скоростей тела 1 и тела 2 в относительном движении применим метод обращения движения, в соответствии с которым мысленно сообщим каждому из звеньев, включая стойку, дополнительное движение
рис. 4.4.1 с угловой скоростью -1.
Тогда в обращенном движении
Для нахождения МЦС к относительным линейным скоростям VO2O1 и Vck восстанавливают перпендикуляры, на пересечении которых получают точку Р. МЦС в относительном движении.
Точка Р. полюс зацепления.
Если зацепляющиеся тела имеют наружные зубья, то полюс Р. расположен между осями О1 и О2 .
Если хотя бы одно из колес имеет внутренние зубья, то полюс Р расположен за линией О1О2.
Сопряженные поверхности поверхности, которые постоянно или с определенной периодичностью входят в зацепление друг с другом.
По отношению к начальным окружностям сопряженные поверхности могут занимать различные положения. Правильным положением является то, которое удовлетворяет основной теореме зацепления, теореме о мгновенном передаточном отношении, которое формулируется:
Общая нормаль, проведенная в точке контакта сопряженных поверхностей, проходит через линию центров О1О2 и делит эту линию на части, обратно пропорциональные отношению угловых скоростей.
Передаточное отношение
(см рис. 4.4.1)
Сопряженные профили должны удовлетворять следующим требованиям:
- быть простыми в изготовлении (технологичными);
- иметь высокий КПД.
Таким требованиям удовлетворят эвольвентные профили.
Эвольвента и ее свойства.
Эвольвента образуется путем перекатывания производящей прямой KyNy без скольжения по основной окружности радиуса rb.
Радиус произвольной окружности ry. ONy ||
Из треугольника ONyKy следует, что
(1)
Т.к. KyNy перекатывается без скольжения по основной окружности, то
rb(y + y) = rb.tg y
y = tg y - y (2)
y = inv y
y инволюта;
Уравнения (1) И (2) являются уравнениями эвольвенты в параметрической форме.
у угол профиля эвольвенты для точки Ку, лежащей на произвольной окружности.
угол профиля эвольвенты для точки К, лежащей на делительной окружности радиуса r.
Угол профиля эвольвенты для точки Кb, лежащей на основной окружности, равен нулю: b=0.
Свойства эвольвенты.
- Форма эвольвенты зависит от радиуса основной окружности. При стремлении rb,эвольвента превращается в прямую линию (пример рейка).
- Производящая прямая KyNy является нормалью к эвольвенте в данной тоске.
- Эвольвента начинается от основной окружности. Внутри основной окружности точек эвольвенты нет.
§4.4 Элементы эвольвентного зубчатого колеса.
Делительной окружностью называется окружность стандартных шага р, модуля m и угла профиля .
Шаг расстояние между одноименными точками двух соседних профилей зубьев, измеренные по дуге соответствующей окружности.
Модулем называется часть диаметра делительной окружности, приходящаяся на один зуб.
Модуль m,[мм] стандартная величина и определяется по справочникам, исходя из трех рядов:
1 ряд наиболее предпочтительный;
2 ряд средней предпочтительности;
3 ряд наименее предпочтительный.
Модуль характеризует высоту зуба. Чем больше зуб, тем более шумной становится зубчатая передача.
Угол профиля угол между касательной к эвольвенте в данной точке и радиус-вектором данной точки (см. чертеж эвольвенты).
Угол профиля для точки, лежащей на делительной окружности, является величиной стандартной и равной 20о (хотя лучше 25о).
Основные расчетные зависимости для определения параметров эвольвентного зубчатого колеса.
Из (1) следует, что радиус делительной окружности
(3)
модуль по ГОСТу определяется
m = p / p = .m (4)
2 .r = p.z
(5)
2 .ry = py.z
(6)
по основной окружности
y = 0 pb = p cos 20o (7)
Виды зубчатых колес.
p = s + e (8)
s = + .m (9)
где коэффициент изменения толщины зуба.
В зависимости от знака коэффициента различают виды зубчатых колес:
- = 0 s = e = p/2 нулевое зубчатое колесо;
- > 0 s > e положительное зубчатое колесо;
- < 0 s < e отрицательное зубчатое колесо.
§4.5 Эвольвентная зубчатая передача и ее свойства (рис. 11-86).
Эвольвентную зубчатую передачу составляют, как минимум, из 2-х зубчатых колес, при этом в рассмотрение вводится две начальные окружности радиусами rw1 и rw2.
Меньшее зубчатое колесо в обычной понижающей зубчатой передаче называется шестерня.
Вместо производящей прямой здесь вводится в рассмотрение линия зацепления N1N2, которая одновременно касается 2-х основных окружностей rb1 и rb2.
Линия зацепления является геометрическим местом точек контакта сопряженных эвольвентных профилей. В точке В1 пара эвольвент, которые в данный момент времени контактируют в точке К, входят в зацепление. В точке В2 этаже пара эвольвент из зацепления выходят.
На линии зацепления N1N2 все взаимодействующие эвольвенты при зацеплении касаются друг друга. Вне участка N1N2 эвольвенты пересекаются, и если такое случится, то произойдет заклинивание зубчатого колеса.
Угол N1O1P = N2J2P = w угол зацепления.
Для передачи, составленной из нулевых зубчатых колес w=20o
Для передачи, составленной из положительных з. к. w>20o
Для передачи, составленной из отрицательных з. к. w<20o
c=c*.m - радиальный зазор, величина стандартная, необходим для нормального обеспечения смазки.
c* - коэффициент радиального зазора, по ГОСТ c*=0.25 (c*=0.35).
Между делительными окружностями у.m это воспринимаемое смещение.
у коэффициент воспринимаемого смещения, он имеет знак, и в зависимости от знака различают:
1. у=0 у.m=0 нулевая зубчатая передача;
2. у>0 у.m>0 положительная зубчатая передача;
3. у<0 у.m<0 отрицательная зубчатая передача;
Свойства эвольвентного зацепления.
- Эвольвентное зацепление молочувствительно к погрешностям изготовления, т.е. при отклонении межосевого расстояния от номинала передаточное отношение зубчатой передачи не изменится.
- Линия зацепления N1N2 является общей нормалью к сопряженным эвольвентным профилям.
- Контакт эвольвент осуществляется только на линии зацепления.
Основные расчетные зависимости для определения основных параметров эвольвентных зубчатых передач.
- Определение угла зацепления.
inv w = inv + (1)
где 1 , 2 изменение толщины зуба;
z1 , z2 число зубьев.
- Определение межосевого расстояния зубчатых передач.
аw = rw1 + rw2 =+= += (2)
z = z1 + z2
- Определение коэффициента воспринимаемого смещения y.
аw = r1 + r2 + y m
=++ y m
y = (3)
Качественные показатели зубчатых передач.
к ним относятся:
- Коэффициент перекрытия .
Характеризует плавность работы зубчатой передачи и показывает, какое число зубьев одновременно участвуют в перекрытии зацепления (насколько одна пара зубьев перекрывает работу другой).
Теоретически может равен 1, и это означает, что как только одна пара зубьев вышла из зацепления, следующая пара сразу же вошла в зацепление.
Если <1, то предыдущая пара зубьев из зацепления вышла, а следующая пара в зацепление не вошла. Такая передача работает с ударами, и ее применение недопустимо. Поэтому конструкторы при проектировании передачи считают минимально допустимым равным 1.05 .
Как правило, эвольвентная зубчатая передача с прямозубыми колесами имеет коэффициент перекрытия =1.1 1.5. Для косозубых колес за счет осевого перекрытия зубьев =+, 1 =2.1 2.5
Зубчатая передача с косозубыми колесами работает более плавно.
- Коэффициент удельного давления .
Характеризует прочностные характеристики передачи с точки зрения контактных напряжений в высшей КП.
- Коэффициент удельного скольжения .
Характеризует износостойкость зубчатой передачи в высшей КП.
Определение коэффициента перекрытия графическим способом.
B1B2 рабочий участок линии зацепления N1N2.
В точке В1 пара эвольвент входит в зацепление, при повороте на угол 1=360о/z1 первая пара эвольвент касается в т. К, а в т.В1 в зацепление вошла следующая пара эвольвент, и участок КВ2 обе пары эвольвент проходят вместе, т.е. вторая пара эвольвент перекрывает работу первой пары. Тогда равен
= ,
где 1 угол перекрытия первого колеса.
1 = rb1
=
Т.к. линия зацепления перекатывается по основной окружности без скольжения, то
= B1B2 , =B1K
=
Способы изготовления зубчатых колес
Существуют два основных способа изготовления зубчатых колес:
- копирование: профиль зуба инструмента (протяжка) переносится, и он оставляет след. Способ очень неточный, малопроизводительный и требует наличие инструмента в большом ассортименте, различаемых по модулю и количеству зубьев. Применяется в мелко серийном производстве.
- огибание (см. лаб.раб. №8): инструменту и заготовке сообщают такое относительное движение, при котором огибающая к положению режущей кромке инструмента очерчивает эвольвенту. Инструмент может быть различным: рейки (гребенки), долбяки и фрезы.
Понятие о производящем исходном контуре реечного инструмента.
Производящий исходный контур проекция режущей грани инструмента на плоскость, перпендикулярную оси вращения заготовки.
Рейка зубчатое колесо с теоретически бесконечно большим количеством зубьев. Как привило, их бывает 8.
rb , поэтому все окружности и эвольвента прямые.
Все параметры по делительной прямой и по прямым, параллельным делительной прямой, стандартизированы.
=20о ; ha* - коэффициент высоты зуба (по ГОСТ ha*=1).
Станочное зацепление.
Станочное зацепление зацепление заготовки и инструмента (см. рис. 10-86).
Параметры, относящиеся к инструменту, имеют индекс o
eo ширина впадины инструмента по делительной прямой,
sо толщина зуба инструмента по делительной прямой.
У инструмента всегда eo = so, rwo = r.
В станочном зацеплении начальная окружность всегда совпадает с делительной окружностью, т.к. необходимо перенести с инструмента стандартные параметры: шаг р, модуль m и угол профиля . Эти стандартные параметры имеют место на делительной окружности или на прямой, параллельной делительной прямой.
По отношению к делительной окружности заготовки, делительная прямая может занимать следующие положения:
- инструмент отодвигается от центра заготовки и между делительной окружностью заготовки и делительной прямой инструмента имеет место смещение х.m, где х коэффициент смещения инструмента, который имеет знак.
В рассматриваемом случае x>0, xm>0 нарезается положительное зубчатое колесо.
Прямая инструмента, касательная к делительной окружности заготовки станочно-начальная прямая.
- делительная прямая инструмента является станочно-начальной прямой, т.е. касается делительной окружности. х=0, хm=0 нулевое зубчатое колесо.
- при смещении инструмента к центру заготовки, между делительной прямой и делительной окружностью смещение xm<0, x<0 отрицательное зубчатое колесо.
Коэффициент изменения толщины зуба :
=2.x.tg
Вопрос: в каком диапазоне может перемещаться инструмент?
где xmin минимальный коэффициент смещения инструмента, при котором наступает подрез зуба.
Если В1 выйдет за N, то будет подрез ( В1 точка пересечения граничной прямой рейки с линией зацепления, а N точка касания линии зацепления с основной окружностью).
zmin минимальное количество зубьев нулевого зубчатого колеса, которое можно нарезать без подреза.
где = 20о , ha* = 1.
Т.к. z должно быть целым, при zmin = 18 гарантировано, что подреза не будет.
Основные расчетные зависимости для определения параметров зубчатого колеса, исходя из схемы станочного зацепления.
- Радиус окружности вершин ra.
ra = r + xm + ha*m уm (1)
уm уравнительное смещение инструмента (расстояние между граничной прямой инструмента и окружностью вершин заготовки).
у вводится в расчет для того, чтобы при создании зубчатой передачи с колесами z1 и z2 было бы обеспечено зацепление этих колес без бокового зазора при стандартном радиальном зазоре.
- Радиус окружности впадин rf.
rf = r ha*m c*m + xm (2)
- Определение высоты зуба.
h = ra rf = 2 ha*m + c*m уm (3)
- Определение коэффициента изменения толщины зуба.
=2.x.tg
Специальные передаточные (планетарные) механизмы.
Планетарным называется механизм, имеющий в своем составе хотя бы одно звено с подвижной геометрической осью в пространстве.
Звено, имеющее подвижную геометрическую ось в пространстве, называется сателит.
Звено, на которое устанавливают ось сателитов, называется водило (Н).
Зубчатые колеса, имеющие неподвижную геометрическую ось в пространстве, называются центральными.
Центральное колесо, имеющее внешние зубья, называется солнечное колесо.
Центральное колесо, имеющие внутренние зубья, называется коронная шестерня (опорное колесо).
Достоинства планетарных передач:
- имеют малые габариты и вес из-за того, что поток мощности, подводимый к центральному колесу, распределяется по к сателитам (к количество сателитов). Затем поток мощности собирается на выходном звене. На одной планетарной передаче можно поставить до 24 сателитов.
- очень высокий КПД, в среднем 0.99.
Недостатки:
Если число сателитов неравно 3, то необходим специальный механизм, который бы выравнивал нагрузку между сателитами. Этот механизм утяжеляет и удорожает конструкцию.
Сравнительный анализ передачи с неподвижными осями планетарной передачи.
На первое колесо подается крутящий момент, а со второго снимают.
Ось В неподвижна Ось В подвижна
u1-2 == u1-Н =
Через число зубьев u1-Н записать нельзя, т.к. ось В подвижная ось.
Чтобы записать передаточное отношение через число зубьев, применим метод обращения движения:
мысленно сообщим всем звеньям механизма, включая стойку, дополнительное движение с угловой скоростью -н. Получим обращенный планетарный механизм с неподвижными осями зубчатых колес.
В обращенном движении звенья этого механизма будут иметь следующие угловые скорости:
1* = 1 Н
2* = 2 + ( Н) = 2 Н
Н* = Н Н = 0
- формула Виллиса
Определение передаточного отношения планетарных механизмов различных схем.
Планетарный однорядный механизм (механизм Джеймса).
КПД в одном ряду 0.99
Передаточное отношение можно определить:
- графическим способом по чертежу;
- аналитическим способом, используя формулу Виллиса.
Графический способ определения передаточного отношения.
Выберем на водиле Н точку F которая расположена на том же расстоянии от оси О2, что и точка А.
Оси О1 и О2 расположены на одном уровне.
Для данной схемы входное звено звено 1 (солнечное колесо), выходным является водило Н.
Зададимся отрезком АА, который изображает линейную скорость колеса 1 в точке А. Т.к. колесо 1 вращается вокруг О1, то закон распределения линейной скорости по первому звену изображается прямой линией О1А. Сателлит 2 в т.А имеет такую же линейную скорость, что и колесо 1. В т.С сателлит 2 имеет МЦС в абсолютном движении, т.к. идет контакт с неподвижным колесом 3. Закон распределения линейной скорости по второму колесу изображается прямой линией СА. В т.В сателлит имеет линейную скорость, которая изображается отрезком ВВ, однако т.В является также и осью водила Н, которое вращается вокруг О2. Следовательно, закон распределения линейной скорости по водилу изобразиться прямой линией О2В. Для точки F водила линейная скорость изображается отрезком FF.
От вертикали до линии распределения скоростей по водилу измеряем угол н, а от вертикали до линии распределения скоростей по колесу 1 измеряем угол 1. Т.к. углы 1 и н отложены от вертикали в одном направлении, то это показывает, что входное звено 1 и выходное звено вращаются в одном направлении.
Аналитический способ определения передаточного отношения.
Применим метод обращения движения, обратив планетарный механизм в непланетарный.
1* = 1 Н
3* = 3 Н = Н
плюсовой механизм.
Планетарный механизм со смешанным зацеплением
(с одним внешним и одним внутренним зацеплением).
при = 0,99
Входное звено первое звено;
Выходное водило.
1 солнечное колесо;
2,3 блок сателлитов;
4 коронная шестерня;
Н водило.
Выберем на выходном звене (на водиле) точку F так, чтобы O1A=O2F (O1 и O2 соосны).
- Графический способ определения передаточного отношения
Отрезок АА' берем произвольно.
- Аналитический способ определения передаточного отношения.
Обратим мысленно планетарный механизм в механизм с неподвижным водилом, для того чтобы использовать формулы для механизма с неподвижными осями зубчатых колес (применим метод обращения движения).
В обращенном движении каждое из звеньев будет иметь:
1 звено: *1 = 1 + (н)
2 звено: *2 = *3 = 2 + (н)
3 звено: *3 = *2 = 3 + (н)
4 звено: *4 = 4 + (н) = н
5 звено: *н = н + (н) = 0
(1)
если (1) переписать через количество зубьев, то
плюсовой механизм
Механизм с двумя внешними зацеплениями.
u(4)1Н = 20 50 при = 0.99
Входное звено водило;
Выходное первое колесо.
u(4)1Н = 1 / u(4)Н1
Например, если u(4)Н1= 20, то u(4)1Н = 1 /20 .
- Графический способ.
Выберем точку F на входном звене так, чтобы O1F = O2B.
Точка С для данной схемы может располагаться как выше, так и ниже точки А. В зависимости от положения точки С план скоростей будет разный.
1 и 2 направлены в разные стороны от вертикали. Следовательно, водило и колесо 1 вращаются в разные стороны.
- Аналитический способ.
Применим метод обращения движения.
u(4)1Н = 1 u(Н)14
Запишем передаточное отношение через число зубьев:
Минусовой механизм
Планетарный механизм с двумя внешними
зацеплениями.
Механизм Давида
Применяется в приборных устройствах, так как u(4)Н1 до 10 000.
Недостаток низкий К.П.Д
- Графический способ.
Выберем на водиле Н точку F так, чтобы O2F=O1A (валы O1 и O2 соосны). Точка С может быть выше или ниже точки А.
FF' произвольный отрезок (линейная скорость точки F).
Для колес 2 и 3 точка С МЦС.
- Аналитический способ.
u(4)1Н = 1 u(Н)14
Минусовой механизм.
Синтез (проектирование) планетарных механизмов.
Под синтезом в этом курсе будем понимать подбор (определение) чисел зубьев планетарных механизмов при условии, что зубчатые колеса нулевые, а радиальный габарит механизма минимальный.
Расчет на прочность не проводим, но он обязательно должен быть проведен при проектировании.
При проектировании конструктор обязан выполнить ряд условий:
- Отклонение от заданного передаточного отношения не должно превышать 10% (5%).
- Обеспечить отсутствие подреза у нулевых зубчатых колес:
У колес с внешними зубьями z1, z2, z3 18 ;
У колес с внутренними зубьями z 85.
Если колеса не нулевые, то zmin до 7 или до 56.
- Обеспечить отсутствие заклинивания в зацеплении сателлит коронная шестерня.
Заклинивания нет, если zкш zсат 8
- Обеспечить выполнение условия соосности входного и выходного звеньев.
- Необходимо обеспечить выполнение условие соседства (окружности вершин соседних сателлитов не должны касаться друг друга).
- Обеспечить выполнение условия сборки. Определить условие сборки, исходя из чертежа невозможно, необходимо проверить выполнение этого условия по уравнению (см. далее).
Проектирование однорядного планетарного механизма.
Дано: u(4)1Н = 6
m = 1 мм
k = 3 количество сателлитов
Определить: z1, z2, z3 ?
при минимальном радиальном габарите;
колеса нулевые.
Зададимся числом зубьев z1 так, чтобы выполнялось условие 2, тогда z1 = 18, z3 = 5 . 18 = 90 85.
Условие соосности записывается в виде
О1В = О2В
r1 + r2 = r3 r2
z1 + z2 = z3 z2
Получим условие соседства.
Условие соседства: окружности вершин соседних сателлитов не касаются друг друга
ВIBII > 2 ra2 (1)
Рассмотрим треугольник O1BIq :
BIBII = 2BIq
2BIq = BIBII = m(z1 + z2) (2)
ra2 = r2 + xm + ha*m ym
Т.к. колеса нулевые, то xm = 0 и ym = 0
ra2 = r2 + ha*m
ra2=(z2+2ha*)
2ra2 = m(z2 + 2ha*) (3)
Подставим (3), (2) в (1)
(4)
Уравнение соседства справедливо для всех схем, только для схем 2, 3 и 4 в знаменателе стоит правая или левая часть условия соосности, а в числителе вместо z2 ставят число зубьев наибольшего из сателлитов.
Условие сборки:
Будем считать, что каждый последующий блок сателлитов устанавливается в позиции ВI.
Чтобы освободить место, нужно повернуть водило на угол (360о / k).
При установке 1го сателлита зубья центральных колес ориентированы относительно оси симметрии.
Если на дуге АВ укладывается целое число шагов, то при повороте водила на угол (360о/k) зубья центральных колес будут ориентированы относительно оси симметрии точно так же, как и при установке первого сателлита.
Если на указанной дуге не укладывается целое число шагов, то при повороте водила на угол (360о / k) зуб 1го колеса не встанет на то же место и тогда, чтобы установить следующий сателлит, нужно от позиции ВII сделать р дополнительных оборотов водила, чтобы за счет выборки углового шага правильно ориентировать зубья центральных колес.
Уравнение сборки имеет вид:
= (1 + kp) = ,где целое число.
Для нашего случая: 18.6 (1+ 3р) / 3 = 36 (1+3р)
Условие сборки выполняется при р = 0.
После подбора чисел зубьев определяют радиусы делительных окружностей колес:
мм
мм
мм
По полученным данным строится схема механизма в масштабе и проверяется выполнение передаточного отношения.
5.3.2 Проектирование планетарного механизма со смешанным зацеплением.
Дано:
m=1 мм
Определить:
z1, z2, z3, z4
при условии:
k=3
радиальные габариты min
колеса нулевые.
Исходная формула:
u(4)1Н = 1 u(Н)14= 1 +
= u(4)1Н 1 = 21 1 = 20
Представим число (20/1) в виде произведений сомножителей:
Где С1~z1 при этом С1, С2, С3, С4 взаимно
С2~z2 простые числа, то есть не имеют
С3~z3 общих делителей.
С4~z4
Указываются все возможные разложения
1: С1= 4 С2= 1 С3= 1 С4= 5
Запишем условие соосности данного редуктора
О1В=О2В
r1 + r2 = r4 r3
m ( z1 + z2 ) = m ( z4 z3 )
В результате преобразований
z1 = C1 ( C4 C3 ) q
z4 = C4 ( C1 + C2 ) q
где q коэффициент пропорциональности любое число но такое, чтобы z было целым.
тогда
z2 = C2 ( C4 C3 ) q
z3 = C3 ( C1 + C2 ) q
z1 = 1 ( 5 1 ) q = 4q z1 = 20
z2 = 4 ( 5 1 ) q = 16q z2 = 80
z3 = 1 ( 1 + 4 ) q = 5q z3 = 25
z4 = 5 ( 1 + 4 ) q =25q z4 = 125
q назначается так, чтобы не было подреза, например q = 5.
Проверяем выполнение условия соседства:
0,87 > 0,82
Условие соседства выполняется.
Проверяем выполнение условия сборки:
= (1 + kp) = (a)
20 . 21( 1+3p) / 3 = 140 при p = 0
Для передач со сдвоенными сателлитами формула (а) не является общей. Общей формулой является:
целое
Условие сборки выполняется.
Если хотя бы одно из условий не выполняется, то необходимо рассмотреть следующий вариант разложения на простые множители.
Если, перебрав все возможные варианты разложения, не удалось подобрать числа зубьев, то допускается изменить заданное передаточное отношение в пределах 10 %.
Для других схем числа зубьев подбираются по формулам, представленным в таблице:
2 внутренних зацепления Схема 3 |
2 внешних зацепления Схема 4 |
|
Условие соосности |
z1 z2 = z4 z3 |
z1 + z2 = z4 + z3 |
z1 |
C1 ( C4 C3 ) q |
C1 ( C4 + C3 ) q |
z2 |
C2 ( C4 C3 ) q |
C2 ( C4 + C3 ) q |
z3 |
C3 ( C1 C2 ) q |
C3 ( C1 + C2 ) q |
z4 |
C4 ( C1 C2 ) q |
C4 ( C1 + C2 ) q |
Кулачковые механизмы.
Кулачковым называется механизм, который содержит два основных звена: кулачок и толкатель, образующих высшую кинематическую пару.
Кулачковые механизмы нашли широкое применение в системах газораспределения ДВС, в системах управления электроцепей в вагонах метрополитена (контроллеры).
Достоинства кулачковых механизмов:
- возможность воспроизведения практически любого закона движения выходного звена;
- малое количество деталей (кулачок и толкатель), что позволяет просто изготавливать и обслуживать.
Недостаток:
наличие высшей кинематической пары, в которой могут возникать повышенные удельные давления, что может привести к разрушению поверхности кулачка.
1 кулачок
2 толкатель
3 ролик
4 пружина
5 контакты
Поверхность кулачка, с которой взаимодействует толкатель рабочий профиль кулачка (действительный).
Поверхность, проходящая через точку В и отстоящая от действительного профиля на расстоянии радиуса ролика теоретический профиль.
§6.1 Основные схемы кулачковых механизмов.
- Кулачковый механизм с поступательно движущимся толкателем.
а) с центральным толкателем (ось толкателя проходит через ось вращения кулачка);
с заостренным
толкателем
б) с внеосным толкателем.
е эксцентриситет
внеосность левая, т.к. ось толкателя проходит справа оси вращения кулачка.
Кулачковый механизм с поступательно движущимся
толкателем.
звено 2 (толкатель) совершает возвратновращающееся движение с центром вращения в точке О2.
Основные параметры кулачковых механизмов.
В процессе работы толкатель совершает в соответствии с рисунком 3 движения:
- поступательно вверх в этом случае толкатель взаимодействует с участком 01;
- стоит на месте (выстой)
контакт с участком 12.
Здесь постоянный радиус кривизны.
- толкатель опускается (сближение) контакт с участком 23.
В первой фазе подъему толкателя (фаза удаления) на профиле кулачка соответствует угол удал;
в фазе выстоя выс;
в фазе сближения сб.удал + выс + сб = раб рабочий угол профиля кулачка.
Угол профиля кулачка можно показать только на кулачке.
Угол поворота кулачка, соответствующий выше указанным фазам перемещения толкателя, определяют, используя метод обращения движения, в соответствии с которым всей системе, включая стойку, мысленно сообщают движение с угловой скоростью (1).Тогда в обращенном движении кулачек становится неподвижным:
*1 = 1 + (1) = 0,
а ось толкателя вместе со стойкой будут перемещаться в направлении (1). И угол поворота кулачка, соответствующий той или иной фазе движения, определяется по углу поворота оси толкателя в обращенном движении на соответствующем участке. Ось толкателя в обращенном движении в любом положении будет касаться окружности радиуса rе.
Поворот кулачка на участке :
01 01 12 12 23 23
рабочий угол поворота кулачка раб:
раб = 01 + 12 + 23
(уб) (выс) (сб)
Всегда независимо от схемы механизма раб = раб, а
уд уд, выс выс, сб сб,
для всех схем, кроме кулачкового механизма с центральным толкателем.
Построение графика перемещений толкателя при заданном профиле кулачка.
Перемещения отсчитываются от начальной окружности радиуса ro.
Точка В принадлежит толкателю, который повора - чивается вокруг оси С, т.е. т.В перемещается по дуге окружности радиусом r = lт. Из точки 1 проводим окружность r = lт до пересечения с окружностью, радиус которой равен расстоянию между тО1 и тС: r = aw. Точка пере сечения т.С1 положение оси вращения толкателя в обращенном движении, когда толкатель контактирует с поверхностью кулачка в
точке 1. Из т.С1 проводим дугу окружности r = lт до пресечения с начальной окружностью. Тогда перемещение точки В будет равным длине дуги 11*. На участке 12 толкатель не перемещается. На участке 23 перемещение точки В ищется аналогично перемещению на участке 01.
№ |
0 |
1 |
2 |
3 |
SB,мм |
0 |
0 |
Понятие об угле давления.
Угол давления угол между вектором линейной скорости выходного звена (толкателя) и реакцией, действующей с ведущего звена (кулачка) на выходное звено. Эта реакция без учета сил трения направлена по общей нормали к взаимодействующим поверхностям. Угол давления определяется экспериментально. Для кулачкового механизма с поступательно движущимся толкателем допустимый угол давления равен: [] = 2535.
Для кулачкового механизма с качающимся толкателем допустимый угол давления равен: [] = 3540.
Реакцию можно разложить на две составляющие: и .
Если, в силу какихлибо причин, угол давления будет увеличиваться, то будет уменьшаться, а увеличиваться.
При достижении углов больше допустимого, возможен перекос оси толкателя в направляющей.
Вывод формулы для определения угла давления в кулачковом механизме.
Из треугольника КВР:
(1)
КР = О1Р О1К = О1 е
КВ = so + sB
(2)
Треугольник О1ВР подобен треугольнику АВС. Тогда
vB1= 1·O1B
Подставим это выражение в (2):
Знак “ ” для правой внеосности;
знак “ + ” для левой внеосности.
Угол давления в кулачковом механизме зависит от размеров кулачковой шайбы: чем она больше, тем угол давления меньше.
Понятие об отрезке кинематических отношений.
Если из точки В для какогото текущего положения толкателя проведем линию, параллельную О1Р, а из центра || nn, то при их пересечении получим точку D:
BD = O1P = vB2 / vB1 =vqB2
Из рисунка следует, что перемещение точки В толкателя и, найдя максимальный отрезок кинематического отношения, можно определить положение центра вращения кулачка, отложив внешним образом от точки D допустимый угол давления.
Синтез (проектирование) кулачковых механизмов по заданному закону движения толкателя.
Под синтезом кулачкового механизма будем понимать построение профиля кулачка, в каждой точке которого угол давления не превышал бы допустимого, а размеры самого профиля были бы минимальны.
Данная задача решается в 3 этапа:
- Строится график заданного закона движения (как правило либо график ускорения точки В толкателя как функция угла положения aB = f(1), либо график линейной скорости точки В vB= f(1)). Требуется построить график перемещения точки В как функцию от угла поворота кулачка sB= f(1).
- Определение минимального размера кулачковой шайбы при условии, что угол давления в любой точке профиля не превышает допустимого.
- Построение профиля кулачка.
Построение закона движения оси толкателя.
Дано: Надо построить:
вид графика aB = f(1), графики aB = f(1)
максимальный ход vB= f(1)
толкателя hт sB= f(1)
b база графика (сколько отводиться на график по оси 1).
Порядок построения:
- Произвольно выбирается база графика.
- Считаем масштаб по оси 1:
, мм/град
- Если задан симметричный вид графика, то:
уд = сб bуд = bсб
В общем случае закон движения может быть несимметричным.
- Зададимся произвольным образом а1= 40 50 мм. Тогда
а2= а1/
Возникает вопрос: каким должно быть расстояние х ?
Его находят из условия равенства площадей под и над осью 1.
Почему надо выдерживать равенство площадей?
Физический смысл площади под кривой ускорения на площадке х скорость толкателя на данном участке.
Физический смысл площади под кривой скорости на участке уд максимальное удаление (перемещение т.В толкателя). Если площади не будут равновеликими, то толкатель, поднявшись на одну величину, опустится на другую.
Построив график ускорения, строим график скорости методом графического интегрирования, выбрав отрезок интегрирования ОК1. Интегрируя график скорости (с отрезком интегрирования ОК2, обычно ОК1=ОК2), получаем график перемещения т.В толкателя. Полученную ломаную линию заменяют плавной кривой.
Расчет масштаба:
(уSВ)max на графике перемещений получается автоматически, и его величина зависит от отрезка ОК2. Тогда, зная ход толкателя, масштаб перемещения будет:
=
Затем в первом приближении принимаем, что кулачок вращается равномерно, тогда угол поворота кулачка пропорционален времени поворота, и оси и t совпадают, но каждая ось имеет свой масштаб.
где b в [мм]; частота вращения кулачка n [об/мин]; раб [град].
Масштаб скорости:
Масштаб ускорения:
Определение минимального радиуса кулачковой шайбы по известному закону движения толкателя.
а) для кулачка с поступательно движущимся толкателем:
Дано: sB=f(1); vB= f(1); []
Определить: ro min
при условии, что угол давления в любой точке профиля кулачка не превышает допустимый.
Порядок построения графика кинематических отношений:
- проводится вертикальная ось sB,мм вдоль которой от произвольно выбранной точки Во (начало отсчета) откладываются отрезки перемещения т.В, взятые с графика sB=f(1). Масштаб по оси s* перемещений может быть равен масштабу графика перемещений s.
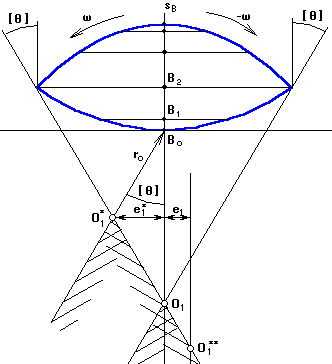
в каждой из полученных точек определяют отрезки кинематических отношений, посчитанные в масштабе s*, и откладывают их под углом в 90 по направлению вращения кулачка.
мм
Там, где отрезок имеет максимальное значение, восстанавливается перпендикуляр, и под углом [] проводится луч.
- Если учитывать реверс, то второй луч проводят под углом [] через отрезок кинематических отношений, отложенный под углом в 90 по направлению реверса и имеющий максимальное значение.
Если реверс не учитывать, второй луч проводят через т.Во под углом []. Если допускается внеосность, то она будет равна е1*. Если внеосность равна нулю, то центр кулачка будет в т.О1:
ro = O1Bo
Если внеосность задана в техническом задании, например левая, то проводят прямую, параллельную прямой О1Во и отстоящая от нее на расстоянии, равном величине внеосности е1, с учетом масштаба s*. В итоге получают точку О1**.
б) для кулачка с качающимся толкателем:
Порядок построения: В произвольном месте выбирается точка Со, из которой радиусом, равным длине толкателя, проводят дугу окружности. По хордам откладывают перемещения т.В. Полученные точки последовательно соединяют с т.Со.
- На этих прямых и на их продолжении откладываются отрезки кинематических отношений, посчитанные в масштабе s* по вышеприведенной формуле. Там, где отрезок имеет максимальное значение, восстанавливается перпендикуляр, и под углом [] проводится луч.
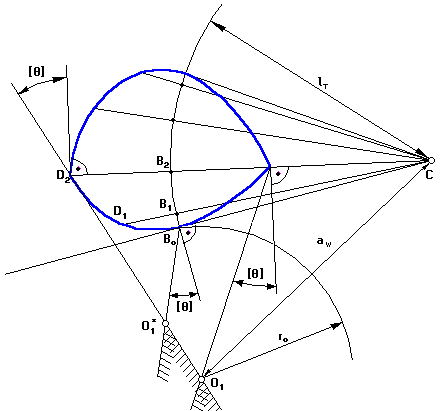
Если учитывать реверс, то второй луч проводят под углом [] через отрезок кинематических отношений, отложенный под углом в 90 по направлению реверса и имеющий максимальное значение. Центр кулачка будет в т.О1*:
ro = O1Bo
Если реверс не учитывать, то второй луч проводят через т.Во под углом []. Центр кулачка будет в т.О1*:
ro = O1*Bo
Построение профиля кулачка.
а) с поступательно движущимся толкателем (рис. 6.5.3.а):
Дано:
ro min, внеосность левая е, раб = раб, к=1, sB = f(1)
Требуется построить профиль кулачка.
В обращенном движении кулачок вращается с угловой скоростью, раной: 1 + (1) = 0.
Порядок построения:
На окружности, радиусом r =ro , проведенной в масштабе l, с левой стороны от оси О1 на расстоянии е выбирается точка Во (пересечение оси толкателя, отстоящей на величину е от точки О1, с окружностью ro min). Точку Во соединяют с центром О1. От полученного луча ВоО1 в направлении (1) откладывают угол раб=раб и проводят луч О1В10. Полученная дуга ВоВ10 делится на 10 равных частей. В каждой из позиций 1,2… проводится положение оси толкателя в обращенном движении, при этом ось толкателя, перемещаясь в направлении (1), будет все время касаться окружности радиуса е, проведенной из центра О1 с учетом масштаба l. В каждой из позиций от точек 1,2,3… откладывают перемещения т.В толкателя вдоль оси толкателя, взятые с графика перемещений с учетом соотношения масштабов l и s. Полученные точки 1*,2*,3*… соединяют плавной кривой и получают центровой или теоретический профиль. Для построения рабочего профиля необходимо знать радиус ролика толкателя. Если он не задан, то его выбирают из конструктивных соображений:
rp=ro min
Кроме того, радиус ролика должен быть таким, чтобы при построении профиля кулачка не было заострения в вершине кулачка. Выбрав радиус ролика, из любых точек теоретического профиля кулачка (чем чаще, тем лучше) проводят дуги окружности r=rp внутренним образом. Проведя огибающую к дугам, получают рабочий профиль кулачка. Если требуется построить профиль кулачка с поступательно движущимся толкателем и внеосностью е=0, то порядок построения профиля будет таким же, только ось толкателя будет проходить через центр вращения кулачка О1.
рис. 6.5.3.а рис. 6.5.3.б
б) с качающимся толкателем (рис. 6.5.3.б):
Дано:
ro min, lт, раб = раб, к=1, sB = f(1), aw (из чертежа для определения ro min)
Требуется построить профиль кулачка.
Порядок построения:
В масштабе l проводятся окружности радиусами ro и aw. В произвольном месте окружности с r = aw выберем т.С0. Соединим точку С0 с точкой О1. От полученного луча в направлении (1) отложим угол раб = раб, получим точку С10. Дугу С0С10 разделим на 10 равных частей (получим точки С1,С2,С3… положение оси толкателя в обращенном движении). Из полученных точек проводим окружности радиусом lт до пересечения с окружностью радиуса ro_min. Из полученных точек 1,2,3… по хордам соответствующих дуг откладывают перемещения т.В толкателя, взятых с графика перемещения с учетом масштаба l. Полученные точки 1*,2*,3*… соединяют плавной кривой теоретический профиль кулачка. Радиусом ролика проводят дуги во внутрь и строят огибающую. Это и есть действительный профиль кулачка.
Теория механизмов и машин